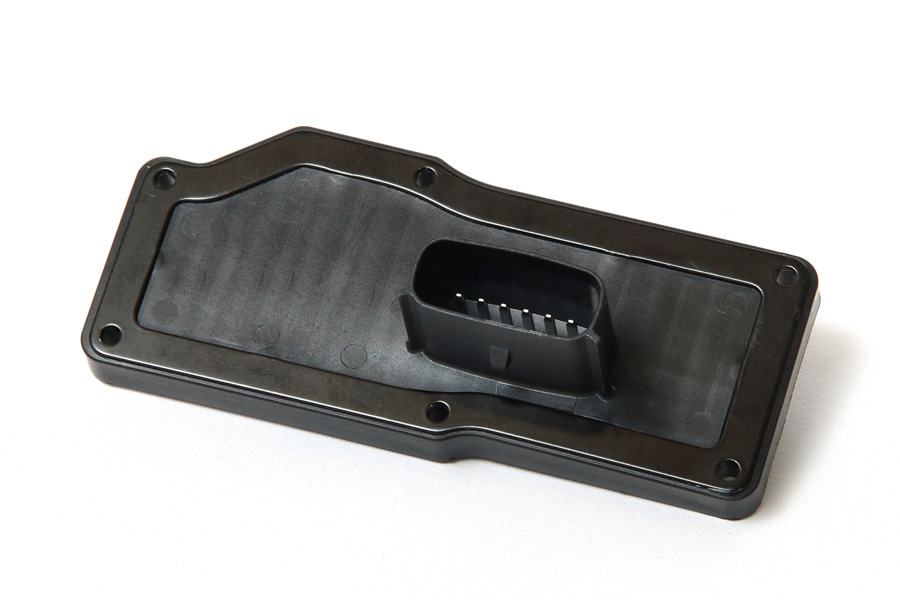
Your blog feed for digital manufacturing resources, in-depth features, and industry news.
Whether you’re in need of buckets for industrial, household, or commercial use, plastic injection molding offers several benefits that make it the go-to choice for manufacturers.
In this article, we’ll explore why plastic injection molding is the best solution for bucket production and how it can benefit your business.
Plastic injection molding is a manufacturing process where melted plastic is injected into a mold cavity under high pressure. Once injected, the plastic solidifies, taking the shape of the mold. This process is used to create a wide variety of plastic products, including buckets of different shapes, sizes, and designs.
Plastic injection molding is highly efficient and scalable, making it ideal for both small and large production runs. It allows for consistent quality and precise control over the final product.
Plastic injection molding is perfect for producing large quantities of plastic buckets quickly and efficiently. Once the mold is created, the production process can run at a rapid pace, making it cost-effective for mass production. This is especially beneficial for businesses that need bulk orders of buckets in a short time.
The cost per unit decreases significantly as production volumes increase. While the initial cost of mold creation can be high, the price per unit becomes much more affordable with larger quantities. If your business requires high volumes of buckets, plastic injection molding is the most cost-effective method in the long run.
One of the biggest advantages of plastic injection molding is the ability to customize bucket designs. Whether you need specific sizes, special handles, or unique shapes, injection molding can accommodate complex designs. You can even integrate features like embossed logos, specialized lids, or reinforced walls for added durability.
Injection molding ensures that each bucket is produced with precision and consistency. The process allows for tight tolerances and uniformity, meaning each bucket will meet the same quality standards. This is especially important if your buckets need to fit specific attachments or need to meet regulatory standards.
Buckets produced using injection molding are strong and long-lasting. The materials used, such as polypropylene (PP) and high-density polyethylene (HDPE), offer excellent resistance to wear and tear, making the buckets durable and able to withstand harsh conditions. These materials are also resistant to chemicals, which is essential for industrial or commercial applications.
Plastic injection molding is a highly efficient process that minimizes material waste. Excess material can often be recycled and reused, making the process environmentally friendly. This is particularly beneficial for companies looking to reduce their carbon footprint and improve sustainability.
Once the mold is ready, the injection molding process can produce buckets quickly. Depending on the size of the bucket and the complexity of the mold, cycle times can be as short as a few minutes per bucket. This means faster production and quicker time-to-market for your products.
Plastic injection molded buckets have a wide range of applications across various industries:
While plastic injection molding offers numerous advantages, there are a few factors to consider before moving forward with production:
Mold Design
The quality of the final product depends heavily on the design and quality of the mold. Complex shapes or intricate features may require more time and investment, so it’s important to collaborate with experienced engineers to ensure the mold meets your specifications.
Material Selection
Choosing the right material for your buckets is critical. Polypropylene (PP) and polyethylene (PE) are commonly used due to their strength, chemical resistance, and flexibility. The material must be chosen based on the specific needs of your buckets (e.g., whether they’ll be used for food, chemicals, or general storage).
Production Volume
Plastic injection molding is most cost-effective for large production runs. If you only need a small batch of buckets, the upfront costs (particularly for mold creation) may be higher. However, for businesses planning to scale, injection molding is the ideal method to achieve economies of scale.
Lead Time
The lead time to produce a mold and begin manufacturing can vary. It’s important to plan ahead and communicate clearly with your injection molding provider about timelines and expectations, especially if you have specific deadlines for product release.
Plastic injection molding is the best method for producing high-quality, durable, and cost-effective buckets at scale. With its ability to create precise, consistent, and customized products, injection molding ensures that your buckets meet your exact specifications while minimizing waste and reducing production time.
Whether you’re looking to produce industrial buckets, food-grade containers, or custom-designed storage solutions, plastic injection molding provides the flexibility and efficiency your business needs to stay competitive.
By choosing plastic injection molding for your bucket production, you can ensure that you get a high-quality, durable product that meets your business needs, all while benefiting from fast production times and lower unit costs for large orders.
Your blog feed for digital manufacturing resources, in-depth features, and industry news.
31 Southlands Road
POLESWORTH
B78 0FL
We will reply to you in 20 minutes.
Our team is online, can be helpful for you.
Our team is online, can be helpful for you.
Didn’t find what you want? Ask our leader for help directly!