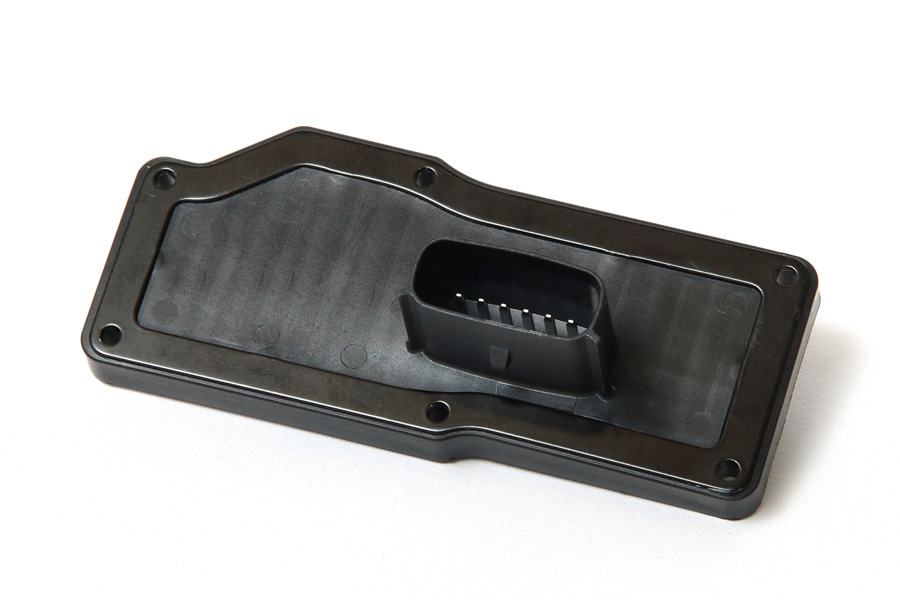
Your blog feed for digital manufacturing resources, in-depth features, and industry news.
Choosing the right mold ensures that the final product meets the desired specifications, while also optimizing manufacturing costs and timelines. In this article, we’ll explore the most common types of molds used for plastic bucket production.
Injection molding is the most widely used method for producing plastic buckets due to its ability to handle high volumes efficiently. In this process, molten plastic is injected into a mold cavity, cooled, and then ejected as a solid plastic part.
Advantages of Injection Molding:
Considerations:
Blow molding is commonly used for creating hollow plastic items, such as plastic buckets with a handle or containers. In this process, plastic resin is heated and inflated inside a mold to form the desired shape.
Advantages of Blow Molding:
Considerations:
Compression molding is a technique that involves placing a plastic material into a heated mold, where it is then compressed to form the desired shape. This method is often used for producing thermosetting plastics, which are heat-resistant and durable.
Advantages of Compression Molding:
Considerations:
Rotational molding (or roto-molding) involves rotating a mold in multiple axes while heating it, allowing the plastic material to melt and coat the mold’s interior. It is commonly used for creating hollow plastic items, including large plastic buckets and containers.
Advantages of Rotational Molding:
Considerations:
Vacuum forming (or vacuum molding) is a process where a heated sheet of plastic is placed over a mold, and air is sucked out to shape the plastic into the mold cavity. This method is mainly used for creating shallow or moderately deep plastic buckets with simple geometries.
Advantages of Vacuum Molding:
Considerations:
Each type of mold used for plastic bucket production has its own set of advantages and limitations, depending on the specific requirements of the product and production volume. Here’s a quick summary:
Understanding the different types of molds available will help you choose the right one for your production needs, ensuring that your plastic buckets are manufactured efficiently, cost-effectively, and with the desired level of quality.
Your blog feed for digital manufacturing resources, in-depth features, and industry news.
31 Southlands Road
POLESWORTH
B78 0FL
We will reply to you in 20 minutes.
Our team is online, can be helpful for you.
Our team is online, can be helpful for you.
Didn’t find what you want? Ask our leader for help directly!