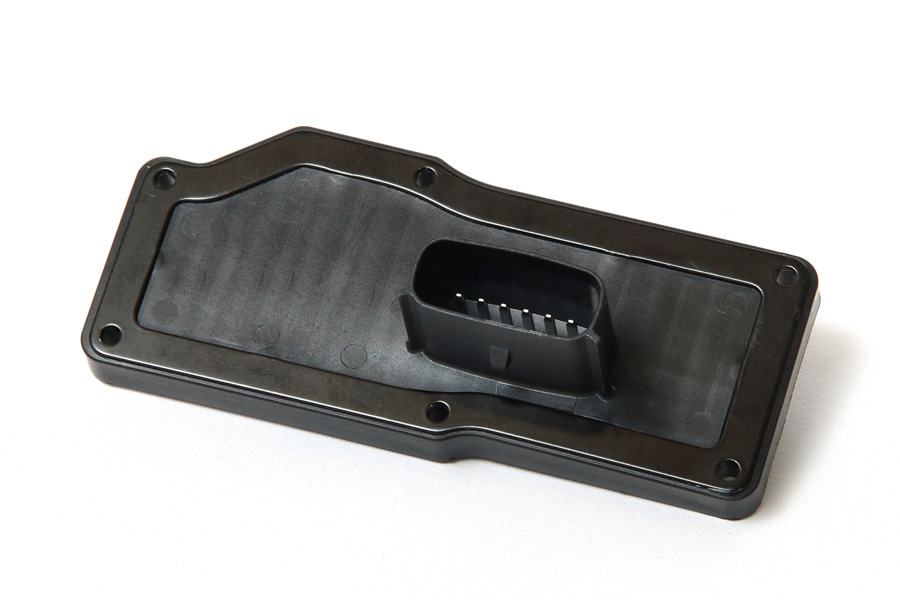
Your blog feed for digital manufacturing resources, in-depth features, and industry news.
A well-tested mold ensures that the final product meets the desired specifications and is free from defects. Whether you’re producing a small batch or a large volume, thorough testing helps identify potential issues early and ensures efficiency in manufacturing.
In this article, we will walk through the essential testing procedures for plastic bucket molds that help maintain high standards in quality and performance.
The first step in mold testing is always a visual inspection. This procedure checks the mold’s external condition for any obvious issues that could affect production. It’s essential to ensure that the mold is clean, free from damage, and has no visible defects.
Key visual checks include:
After a visual inspection, the next step is to perform a trial run. This involves running the mold through the injection molding machine to produce a test batch of plastic buckets. The aim is to evaluate how well the mold performs under real production conditions.
Key trial run checks include:
Once the trial run has produced test buckets, it’s important to check the dimensional accuracy of the finished products. The mold must produce plastic buckets that adhere to strict specifications regarding size, shape, and wall thickness.
Key dimensional checks include:
Ensuring proper material flow and venting is crucial for avoiding defects like air pockets or short shots in the final product. During this stage, it’s important to assess the mold’s ability to handle plastic flow and air removal.
Key tests include:
Once the bucket is formed, it’s essential to test the strength and durability of the plastic. A high-quality mold should produce a product that can withstand its intended use.
Key stress and durability tests include:
The surface finish of a plastic bucket is an important indicator of mold quality. Imperfections like scratches, dents, or discolorations can result from improper mold design or insufficient maintenance.
Surface finish tests include:
After ensuring that the plastic buckets meet quality standards, the mold should be subjected to extended cycle tests to simulate full-scale production. This test checks the mold’s reliability and efficiency over a large number of cycles.
Key cycle testing includes:
After conducting the tests, the mold may require adjustments to correct any issues that were discovered during the testing process. Regular maintenance is also essential to ensure the mold remains in optimal condition for long-term use.
Post-testing adjustments include:
Testing is a critical part of the mold production process, ensuring that plastic bucket molds perform at their best and produce high-quality products. By following these detailed testing procedures, manufacturers can identify potential issues early, improve the efficiency of the production process, and deliver reliable, durable plastic buckets that meet customer expectations.
Whether you’re designing new molds or improving existing ones, investing time in thorough testing is essential to maintaining high standards in the plastic injection molding industry.
Your blog feed for digital manufacturing resources, in-depth features, and industry news.
31 Southlands Road
POLESWORTH
B78 0FL
We will reply to you in 20 minutes.
Our team is online, can be helpful for you.
Our team is online, can be helpful for you.
Didn’t find what you want? Ask our leader for help directly!