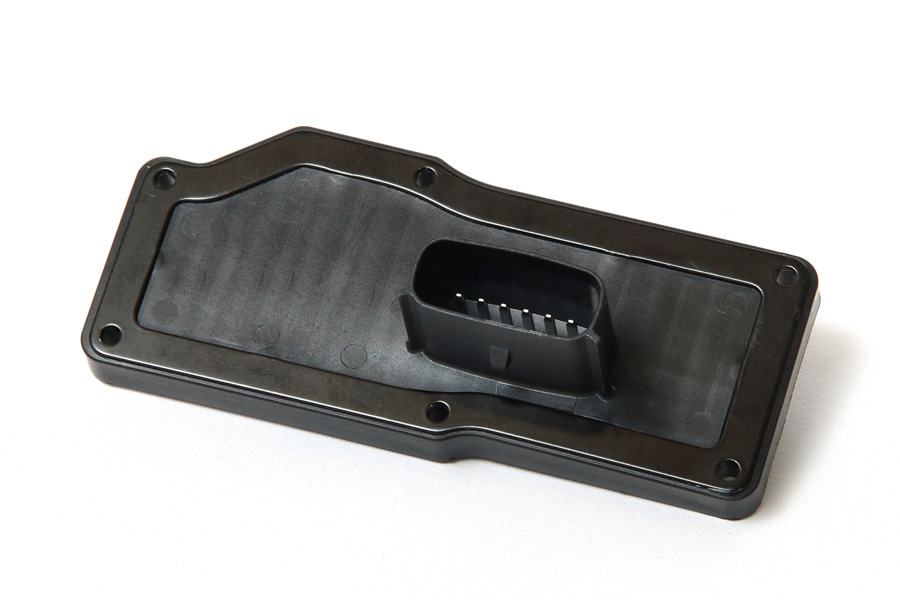
Your blog feed for digital manufacturing resources, in-depth features, and industry news.
The quality, durability, and efficiency of the mold directly impact the production process, as well as the final product. In this article, we will explore the most commonly used materials for plastic bucket molds and why they are essential to ensuring high-quality production.
Steel is by far the most widely used material for plastic bucket molds due to its excellent properties and versatility. Steel molds are known for their strength, durability, and longevity, making them ideal for high-volume production.
Advantages of Steel Molds:
Types of Steel Used:
Aluminum is another material used for plastic bucket molds, particularly for low to medium-volume production. While not as durable as steel, aluminum offers some distinct advantages that make it a good option in certain situations.
Advantages of Aluminum Molds:
Considerations:
Copper-alloy steel is a special type of steel that contains a higher proportion of copper. This material is particularly beneficial in applications that require excellent heat resistance and thermal conductivity.
Advantages of Copper-Alloy Steel Molds:
Use Cases:
Beryllium copper is another high-performance material used in mold production. It is an alloy of copper and beryllium, known for its high thermal conductivity and strength.
Advantages of Beryllium Copper Molds:
Considerations:
Tool steel is a category of carbon and alloy steels that are specifically designed for the manufacturing of molds and dies. It is known for its strength, hardness, and wear resistance.
Advantages of Tool Steel Molds:
Common Types of Tool Steel:
Stainless steel is a highly corrosion-resistant material, which makes it ideal for molds that will be used in environments where moisture or chemical exposure is a concern.
Advantages of Stainless Steel Molds:
Considerations:
The material used for plastic bucket molds plays a crucial role in determining the quality, durability, and efficiency of the production process. The right choice of material depends on factors such as production volume, cost, heat resistance, and the complexity of the mold design.
By choosing the right material for your plastic bucket molds, you ensure efficient production, minimize defects, and achieve high-quality products every time.
Your blog feed for digital manufacturing resources, in-depth features, and industry news.
31 Southlands Road
POLESWORTH
B78 0FL
We will reply to you in 20 minutes.
Our team is online, can be helpful for you.
Our team is online, can be helpful for you.
Didn’t find what you want? Ask our leader for help directly!