Plastic injection molding is one of the most versatile and efficient manufacturing processes used in industries today. It’s a technique that allows for the mass production of high-precision plastic parts and components in a variety of shapes, sizes, and complexities. Whether you’re creating intricate parts for the medical sector, automotive components, or everyday consumer products, plastic injection molding is an essential technology that drives modern manufacturing forward.
What Makes Plastic Injection Molding So Essential?
The process begins with a high-quality plastic resin, which is heated and injected into a precisely designed mold under high pressure. Once cooled, the result is a durable and highly accurate plastic product. But it’s not just the technicality that makes injection molding indispensable—it’s the vast array of benefits it offers businesses across multiple sectors. From cost efficiency to speed and scalability, this method provides a solution for companies seeking mass production without sacrificing quality.
In this guide, we’ll walk you through the core processes of plastic injection molding, explore the manifold benefits it offers, and discuss the wide-ranging applications that make it indispensable across industries—from automotive and medical devices to consumer electronics and beyond.
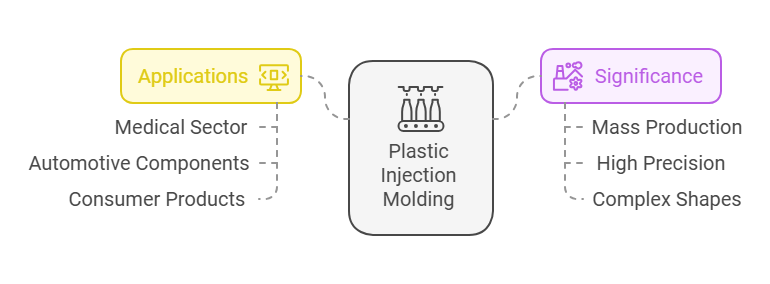
What is Plastic Injection Molding?
Understanding the Basics of Plastic Injection Molding
At its core, plastic injection molding is a manufacturing process used to create intricate plastic parts by injecting molten plastic into a mold under high pressure. The beauty of injection molding lies in its precision, speed, and cost-effectiveness for mass production.
The general process flow involves four key stages:
- Melting: Plastic material (often in the form of pellets or granules) is fed into a heated barrel. The material is then melted into a liquid form by the combined action of heat and pressure.
- Injection: The molten plastic is forced into a mold cavity through a nozzle under high pressure. The mold is designed to shape the plastic into the desired part. The injection process typically takes just a few seconds, making it fast and efficient.
- Cooling: Once the mold is filled, the plastic is allowed to cool and solidify. Cooling time can vary depending on the size and complexity of the part, but it’s crucial for ensuring the integrity and dimensional accuracy of the molded product.
- Solidifying: After cooling, the plastic has hardened into the shape of the mold, and the part is ejected. At this stage, the part is ready for further processing, such as trimming, painting, or assembling, if needed.
How Does Plastic Injection Molding Work?
Plastic injection molding is a precise, multi-step process that involves several key components working in tandem to produce high-quality plastic parts. Let’s break down the steps in more detail:
- Injection Molding Machine: This is the heart of the process. The machine has two primary functions: melting the plastic and injecting it into the mold. The injection molding machine consists of a hopper (which feeds the raw plastic), a barrel (where the plastic is melted), a screw (which mixes and moves the melted plastic), and a plunger (which injects the plastic into the mold cavity).
- Molds: Molds are custom-made, typically from steel or aluminum, and they determine the shape of the final product. The mold consists of two halves: the core and the cavity. The molten plastic fills the cavity, which forms the part. Precision in mold design ensures the final product matches exact specifications.
- Materials: The choice of material plays a significant role in the molding process. Most commonly, thermoplastics (like ABS, polycarbonate, or polypropylene) are used, but thermosetting plastics and elastomers can also be molded. The material is selected based on factors such as strength, flexibility, and thermal resistance, depending on the application.
- Cooling and Ejection: Once the plastic is injected into the mold and begins to cool, the part solidifies. When the part is sufficiently cooled, the mold halves open, and the part is ejected. Ejection pins, or air blasts, may be used to gently remove the part from the mold cavity without damaging its intricate features.
Each of these steps is carefully controlled to ensure the production of high-quality, consistent parts that meet the precise specifications of the customer. This efficiency, paired with the ability to work with a wide range of materials, makes injection molding an ideal choice for industries seeking both large-scale production and tight tolerances.
Common Types of Plastic Injection Molding Machines
Choosing the Right Injection Molding Machine for Your Needs
Selecting the right injection molding machine is a crucial decision that impacts the efficiency, cost, and quality of production. There are several types of machines to choose from, each designed for specific purposes and production environments. Let’s break down the three most common types:
- Horizontal Injection Molding Machines
The most commonly used type, horizontal injection molding machines feature a horizontal arrangement of the injection unit and mold. In these machines, the plastic material is injected into the mold cavity from the side. Horizontal machines are ideal for large, heavy molds and are used in a wide variety of industries, including automotive, consumer goods, and packaging. They’re well-suited for high-volume production and can accommodate a wide range of mold designs. - Vertical Injection Molding Machines
Vertical injection molding machines, as the name suggests, have a vertical configuration. In these machines, the injection unit and mold are arranged vertically, with the material being injected from above. Vertical machines are ideal for producing smaller parts or those requiring overmolding (when one material is molded over another), as they allow for easier stacking and integration of multiple components. They’re commonly used in applications like electronics, medical devices, and automotive parts that require intricate, multi-component designs. - Electric Injection Molding Machines
Electric injection molding machines are powered entirely by electric motors, as opposed to hydraulic or mechanical systems. These machines offer higher precision and faster cycle times compared to traditional machines. They are energy-efficient and produce less noise and heat, making them ideal for high-precision industries such as medical device manufacturing, packaging, and electronics. Although they may have a higher initial cost, their lower operational costs and environmental benefits make them an increasingly popular choice for many companies.
Factors to Consider When Selecting the Best Machine for Your Production
When choosing an injection molding machine, several factors need to be taken into account:
- Part Size and Complexity: Consider the size and intricacy of the parts you need to produce. Larger, more complex parts might require a horizontal machine, while smaller, multi-component parts may be better suited for vertical machines.
- Cycle Time and Production Volume: The speed at which the machine can cycle (injecting, cooling, and ejecting parts) is crucial. If you require high-speed production and short cycle times, electric machines are a solid choice. For larger volumes, horizontal machines may be more appropriate.
- Material Requirements: Different machines handle different materials. Ensure that the chosen machine can handle the materials you plan to use, whether they are thermoplastics, elastomers, or others. For specialized materials, electric machines may offer the most precise control.
- Cost Considerations: While electric machines tend to be more expensive initially, they often save money in the long run due to lower energy costs and faster cycle times. If you’re working with smaller volumes, a vertical or horizontal machine may offer a better return on investment.
- Automation and Integration: Many modern injection molding machines offer advanced automation options, such as robotic arms for part ejection, material handling, or quality control. If automation is key to your production process, look for machines that support these features.
How Injection Molding Machines Impact Production Efficiency
The technology behind injection molding machines has come a long way in recent years, with significant advancements in automation, precision, and speed. These innovations have revolutionized the industry, improving both efficiency and product quality. Here’s how modern injection molding machines impact production efficiency:
- Advanced Technology for Enhanced Precision
Modern injection molding machines are equipped with advanced technologies that allow for higher precision and tighter tolerances. Features such as closed-loop control systems, digital sensors, and servo-driven motors help monitor and control every aspect of the molding process, ensuring consistent quality and reducing waste. The result is not only improved part quality but also the ability to create more intricate and complex designs. - Automation in Injection Molding
Automation plays a pivotal role in improving production efficiency. Automated systems can handle everything from loading materials into the machine to removing finished parts. Robotic arms and conveyors increase the speed and precision of part ejection, reducing the need for manual labor and decreasing human error. Automated systems also enable continuous, 24/7 production with minimal downtime, which is crucial for high-volume manufacturing. - Faster Cycle Times
Advances in injection molding technology, particularly in electric machines, have significantly reduced cycle times. Faster cycle times mean that machines can produce more parts per hour, increasing throughput and reducing lead times. This is especially important in industries where speed to market is a competitive advantage. The reduction in cycle time also helps reduce energy consumption per unit produced, improving cost efficiency. - Energy Efficiency and Cost Savings
Newer injection molding machines, especially electric ones, consume less energy compared to traditional hydraulic machines. By using energy-efficient motors and servo-driven systems, manufacturers can reduce operating costs while maintaining high-speed production. Additionally, the precise control offered by these machines reduces material waste and lowers overall production costs. - Predictive Maintenance
Modern machines often come equipped with sensors and diagnostic tools that allow for predictive maintenance. By monitoring key components and tracking performance data, manufacturers can predict when maintenance is needed before a failure occurs, reducing unplanned downtime and improving overall machine reliability.
In summary, the choice of injection molding machine can have a profound effect on production efficiency. By leveraging the latest advancements in technology, manufacturers can streamline operations, improve precision, reduce waste, and ultimately produce higher-quality parts in less time and at a lower cost.
Key Advantages of Plastic Injection Molding
Cost Efficiency in Large-Scale Production
One of the standout advantages of plastic injection molding is its cost efficiency in large-scale production runs. When it comes to manufacturing high volumes of parts, injection molding shines as a reliable, cost-effective solution. Once the mold is designed and fabricated, the cost per part decreases significantly with each additional unit produced. This makes injection molding an ideal choice for mass production, as it delivers consistent results at a relatively low per-unit cost.
Mass Production Efficiency:
The initial cost of designing and producing the mold can be high, but once it’s in place, the cost of manufacturing each part diminishes rapidly as production scales up. This makes injection molding far more economical than many alternative manufacturing methods, such as CNC machining or 3D printing, where the cost per part remains relatively high even at larger volumes due to the time and labor involved in each piece’s production.
- 3D Printing: While 3D printing is excellent for prototypes and low-volume, highly customized parts, it doesn’t offer the same cost-saving benefits at scale. Each 3D-printed part requires additional time for printing, layering, and post-processing, making it less suitable for large-scale production.
- CNC Machining: CNC machining is more accurate and versatile for creating parts from solid materials, but it’s often more time-consuming and expensive compared to injection molding, especially when producing high volumes. Machining requires more manual setup, tool changes, and labor for each part, leading to higher costs and longer production times for large runs.
Long-Term Savings:
With injection molding, the savings become especially evident when producing hundreds of thousands or even millions of parts. The ability to automate the process with minimal human intervention, coupled with the rapid cycle times of modern machines, ensures cost reductions and maximizes profitability over time.
Versatility in Material Use
Plastic injection molding is incredibly versatile when it comes to the types of materials that can be used, making it suitable for a wide range of applications across different industries. The process can accommodate a vast array of plastics, thermoplastics, and even some thermosetting materials, each offering unique properties suited to various product needs.
Types of Materials Used in Injection Molding:
- Thermoplastics: The most commonly used materials in injection molding, thermoplastics can be melted and re-melted without degradation. Examples include ABS (Acrylonitrile Butadiene Styrene), polycarbonate, polypropylene, and nylon. These materials are highly versatile, offering a balance of strength, flexibility, and durability, and are used in applications ranging from automotive parts to consumer electronics.
- Thermosetting Plastics: While less common, thermosetting plastics, such as epoxies and phenolics, are used when parts need to retain their shape after being heated and set. These materials are ideal for applications that require resistance to heat and chemical corrosion, such as electrical components and medical devices.
- Elastomers: Used for producing flexible, rubber-like parts, elastomers like thermoplastic elastomers (TPE) and silicone are increasingly popular in industries such as medical devices, automotive, and electronics, where high elasticity and resilience are required.
Material Selection and Process Control: Choosing the right material for injection molding is crucial, as it directly affects the final product’s performance, cost, and appearance. The properties of each material—such as strength, flexibility, chemical resistance, and thermal stability—should be aligned with the requirements of the end-use application. Material selection also impacts cycle time, mold design, and overall cost, so understanding the material’s characteristics and how it interacts with the injection molding process is essential for optimizing production.
High Precision and Complex Designs
One of the most compelling advantages of plastic injection molding is its ability to produce parts with high precision and complex geometries. Whether you’re manufacturing small, intricate components or large, detailed parts, injection molding offers unmatched accuracy and consistency in part production.
Intricate Part Design: Injection molding enables the creation of parts with very fine features, such as thin walls, undercuts, and intricate patterns, which would be difficult or impossible to achieve with other manufacturing methods like CNC machining or casting. The precision of injection molding ensures that even the smallest details—such as sharp edges, small holes, and fine threads—are replicated perfectly across all parts.
This makes injection molding especially beneficial for industries that require high-performance parts with fine tolerances, including:
- Automotive Industry: The ability to create lightweight, durable, and highly detailed components, such as dashboards, bumpers, and engine parts, makes injection molding indispensable in automotive manufacturing. Precision molding allows for the production of parts that fit together seamlessly, reducing the need for post-production modifications.
- Medical Devices: Medical devices require parts that are not only precise but also safe and reliable. Injection molding ensures that medical components, from surgical instruments to drug delivery devices, are produced to the highest standards of accuracy and cleanliness.
- Electronics: The growing demand for smaller, more complex electronic devices has made plastic injection molding a critical technology in the production of items like smartphone casings, connectors, and circuit boards. The ability to mold complex features like micro-channels, thin walls, and integrated clips helps manufacturers create compact, high-performance products.
Consistency and Repeatability:
In addition to producing high-precision parts, injection molding excels at producing them consistently. Once the mold is designed and optimized, the injection molding process can repeat the same design thousands, or even millions, of times without sacrificing quality. This consistency ensures that each part produced meets the same specifications and is ready for use without requiring additional quality checks or revisions.
The combination of precision, complex design capability, and repeatability makes plastic injection molding the go-to process for producing parts with the highest level of detail and performance across multiple industries. Whether you need a handful of prototypes or mass production quantities, injection molding guarantees both quality and cost-effectiveness.
Plastic Injection Molding in Different Industries
Automotive Applications of Plastic Injection Molding
In the automotive industry, plastic injection molding is a key technology for producing lightweight, durable, and cost-effective components. The demand for higher fuel efficiency, lower emissions, and more complex designs has driven automakers to increasingly rely on injection molding for a wide variety of parts.
Lightweight Components for Fuel Efficiency:
The automotive industry has a growing need for lightweight materials that can reduce overall vehicle weight and, consequently, improve fuel efficiency and reduce carbon emissions. Plastic injection molding provides the ideal solution by enabling the production of lightweight, high-strength parts such as dashboard components, bumpers, exterior panels, and engine covers. These parts can be made from various thermoplastics like polycarbonate, ABS, and polypropylene, all of which offer excellent strength-to-weight ratios.
Durability and Performance:
Plastic parts produced via injection molding also offer outstanding durability, making them suitable for automotive applications that endure high stress, heat, and exposure to chemicals. Examples include under-the-hood parts, lighting components, and fuel system parts. The molding process ensures consistent quality and strength in every piece, essential for maintaining vehicle safety and longevity.
Customization and Complex Designs:
Injection molding allows automakers to create parts with complex geometries and integrated features, such as built-in clips, snap-fit connectors, and overmolding (combining two materials in a single part). These features help reduce assembly time and the number of parts required for a final product, which contributes to cost savings. Additionally, manufacturers can create customized components with precise fitments, improving the overall design of the vehicle and enhancing its performance.
Medical Device Manufacturing with Plastic Injection Molding
In the medical device industry, plastic injection molding plays a vital role in producing precise, sterile, and high-performance components that are crucial for patient safety and product reliability.
Precision for Critical Applications:
Medical devices require extreme precision to ensure proper functionality and patient safety. Injection molding offers the ability to create complex, high-tolerance parts with fine details, such as surgical instruments, drug delivery systems, catheters, and implants. Advanced features, such as microfluidic channels for diagnostics or drug administration, can be easily incorporated into the design, making injection molding essential for this industry.
Sterility and Cleanliness:
Another crucial aspect of medical device manufacturing is sterility. Plastic injection molding allows for the production of parts in a controlled, clean environment. Medical-grade polymers such as polyethylene, polypropylene, and PEEK (polyetheretherketone) are commonly used because they are biocompatible and resistant to contamination. These materials are molded with precision and are easy to sterilize, making them perfect for medical applications.
Compliance and Quality Control:
Medical device manufacturers must adhere to strict regulations set by organizations such as the FDA (U.S. Food and Drug Administration) and ISO 13485. Injection molding ensures that components meet the highest quality standards, with processes in place for quality control, traceability, and compliance with regulatory requirements. Features such as automated inspection systems help ensure that each part is free from defects and meets safety standards.
Customization and Innovation:
The ability to create highly customized medical components is another advantage of injection molding. Whether it’s a specialized handle for a surgical tool, a custom-shaped injection needle, or a wearable medical device, injection molding allows manufacturers to create tailor-made solutions that meet the unique needs of patients and healthcare providers.
Consumer Products and Electronics: The Role of Injection Molding
Plastic injection molding is crucial to the production of consumer goods and electronic components, offering manufacturers a reliable and cost-effective way to create high-quality products quickly and at scale.
Consumer Goods:
From household items like bottles, toys, and kitchenware to furniture and personal accessories, injection molding is used to produce a wide range of consumer products. The process allows for the efficient creation of complex shapes with high levels of detail and aesthetic appeal. With the ability to produce consistent, high-quality parts, manufacturers can meet consumer demands for durability and design. Injection molding also supports the creation of colorful and textured surfaces that are highly appealing in consumer-facing products.
Cost-Effective Mass Production:
For consumer goods, which often require large production runs, injection molding is an incredibly cost-effective solution. The ability to create thousands, even millions, of identical items from a single mold makes it the go-to choice for manufacturers in high-volume industries. Additionally, because the cycle time for each part is short, injection molding helps keep production times and costs low, ensuring that companies can meet market demand quickly.
Electronics:
Injection molding is also essential in the production of electronic components, such as smartphone casings, remote controls, laptop covers, connector housings, and protective enclosures. The need for high precision and thin-walled designs makes injection molding an ideal fit for electronics manufacturing, where intricate features, like button molds, vents, and ports, are often required. Thermoplastics like ABS and polycarbonate are used for their strength, heat resistance, and electrical insulating properties, which are critical for protecting sensitive electronic components.
Complex and Custom Designs:
In the consumer electronics sector, many products require intricate, compact designs. Injection molding allows for the integration of multiple features into a single molded part, reducing the need for secondary assembly processes and cutting down on production time and costs. Additionally, overmolding and insert molding techniques enable the combination of different materials, such as rubber and plastic, to create components that are both functional and aesthetically pleasing.
Durability and Safety:
In electronics, product safety and durability are paramount. Injection molding ensures that parts are manufactured with uniform consistency, reducing the risk of defects that could lead to device malfunction. Additionally, injection-molded parts offer superior resistance to wear and tear, heat, and shock, which is crucial for ensuring the longevity of consumer products and electronics.
In summary, plastic injection molding is an indispensable technology across many industries, including automotive, medical devices, and consumer electronics. Its ability to produce lightweight, precise, complex, and high-quality parts makes it the go-to solution for companies looking to optimize production, reduce costs, and meet the growing demand for innovative, reliable products. Whether it’s for safety-critical medical equipment, durable automotive components, or sleek consumer electronics, injection molding plays a central role in shaping modern manufacturing.
Common Injection Molding Defects and How to Avoid Them
Identifying and Solving Common Defects in Plastic Injection Molding
In plastic injection molding, despite its efficiency and precision, defects can still occur during production. These defects can affect the quality, functionality, and appearance of the final product, which may lead to increased costs, delays, and waste. Being able to identify and address common injection molding defects is essential for maintaining the quality of the finished parts.
1. Warping:
Warping occurs when a molded part cools unevenly, causing it to distort or become misshapen. This often happens if the cooling process is inconsistent or if the material contracts unevenly after injection.
- Solutions:
- Optimizing Cooling Time and Temperature: Adjust the cooling time and temperature distribution to ensure even cooling throughout the mold.
- Mold Design Adjustments: Ensure the mold design promotes uniform cooling, especially in thicker areas where material may cool more slowly.
- Material Selection: Choose materials with lower shrinkage rates or those designed for better dimensional stability, such as polycarbonate or ABS.
2. Sink Marks:
Sink marks are depressions or dimples that appear on the surface of a molded part. They are typically caused by the material shrinking during cooling, often in thicker sections of the part where cooling is slower.
- Solutions:
- Modify Part Design: Reduce wall thickness in areas prone to sink marks or use ribs to reinforce sections without increasing thickness.
- Increase Injection Pressure: Increasing the injection pressure can help pack the material into the mold more effectively and reduce the likelihood of shrinkage.
- Control Cooling Time: Adjusting the cooling time can help ensure that the material cools uniformly across the part, reducing the chances of sink marks.
3. Flash:
Flash occurs when molten plastic leaks out of the mold cavity during injection, causing unwanted thin edges or excess material to form around the part.
- Solutions:
- Check Mold Clamping Force: Ensure that the clamping force is adequate to hold the mold tightly together during injection, preventing plastic from escaping.
- Inspect Mold Alignment: Ensure the mold is properly aligned and that there are no gaps between the mold halves where plastic could escape.
- Control Injection Pressure: Excessive injection pressure can cause flash. Reduce pressure or modify injection speed to avoid overpacking the mold.
4. Short Shots:
Short shots occur when the mold does not fill completely, leaving gaps or voids in the part. This can happen due to insufficient injection pressure, poor material flow, or a clogged gate.
- Solutions:
- Increase Injection Pressure: Increasing the pressure ensures that enough material flows into the mold to completely fill the cavity.
- Optimize Gate Design: Use appropriately sized gates to allow better flow of material into the mold.
- Improve Mold Venting: Ensure the mold is properly vented to allow air to escape and prevent premature solidification of the material.
By identifying these common defects early in the production process and implementing preventive measures, manufacturers can greatly reduce the risk of defects, minimize downtime, and produce high-quality molded parts consistently.
Quality Control in Injection Molding
Quality control is critical to ensuring that injection-molded parts meet the necessary standards for precision, performance, and aesthetics. Inconsistent mold designs, improper material selection, and inaccurate machine calibration can all lead to defects that compromise product quality. Therefore, a robust quality control process is essential at every stage of injection molding.
1. Mold Design:
The mold design is fundamental to the success of any injection molding process. Proper mold design ensures that the material flows correctly into the mold cavity, cools evenly, and has the right amount of pressure applied throughout the injection cycle.
- Key Considerations:
- Gate and Runner Design: Ensure the gates and runners are properly sized to allow smooth material flow, avoiding problems like short shots and air pockets.
- Cooling System: Properly designed cooling channels help maintain uniform cooling rates, preventing defects like warping or sink marks.
- Ventilation: Effective venting ensures that air is expelled during the injection process, preventing trapped air from causing defects.
2. Material Selection:
Selecting the right material for the application is crucial in ensuring that the final product meets the desired characteristics, such as strength, flexibility, and resistance to environmental factors. Material quality also impacts the molding process itself, as certain materials behave differently under heat and pressure.
- Key Considerations:
- Material Compatibility: Ensure the material chosen is compatible with both the part design and the molding process.
- Material Testing: Conduct thorough testing of materials to check for properties like shrinkage rate, viscosity, and tensile strength to ensure they meet specifications.
- Batch Consistency: Source materials from reliable suppliers to avoid variations in material quality that could impact the final product.
3. Machine Calibration:
Proper machine calibration is vital for ensuring that the injection molding machine operates at optimal efficiency. Inaccurate machine settings can lead to defects such as uneven cooling, flash, and dimensional variations.
- Key Considerations:
- Injection Pressure and Speed: Calibrate the injection pressure and speed to match the material and mold requirements, ensuring uniform filling and packing of the cavity.
- Temperature Control: Accurately control the temperature of the mold and material to maintain consistency and avoid issues like premature solidification or excessive cooling.
- Cycle Time: Adjust the cycle time to ensure that parts are given sufficient time to cool and solidify, preventing issues like warping or shrinkage.
4. In-Process Inspections and Testing:
Continuous monitoring of the injection molding process through in-process inspections and testing ensures that any deviations are identified and addressed before defects are produced. Automated inspection systems, such as vision systems and pressure sensors, can monitor factors like part dimensions, material flow, and mold temperature in real-time.
- Key Considerations:
- Automated Quality Checks: Use automated inspection technologies to check part dimensions, surface finish, and overall quality during the production process.
- Statistical Process Control (SPC): Implement SPC techniques to monitor key production metrics and ensure that any variation is detected early and corrected before it affects the product.
By integrating advanced mold design, material selection, and machine calibration with ongoing quality control throughout the production process, manufacturers can ensure that their injection-molded parts meet high-quality standards, reducing defects and improving overall product consistency.
Cost Factors in Plastic Injection Molding
Breakdown of Injection Molding Costs
Plastic injection molding is a highly efficient and cost-effective manufacturing process, but several factors contribute to its overall cost structure. Understanding these cost factors can help businesses optimize production and maximize their return on investment. Here’s a breakdown of the main cost components in injection molding:
1. Mold Design and Fabrication Costs:
The mold is one of the largest upfront costs in injection molding. It’s typically made from high-quality steel or aluminum, and its design must be precise to ensure proper part formation. The complexity of the mold and the number of cavities can significantly affect the cost.
- Factors Affecting Mold Costs:
- Design Complexity: The more intricate the mold design, the higher the cost. Features like undercuts, complex geometries, or multiple cavities require more advanced mold design and manufacturing.
- Mold Material: Molds made from durable materials like H13 steel or P20 steel are more expensive but provide greater longevity and wear resistance.
- Mold Size: Larger molds require more material and machining time, increasing costs.
2. Material Selection:
The material used for injection molding plays a significant role in determining the overall cost of production. Common materials include ABS, polycarbonate, polypropylene, and nylon, but each material comes with its own cost structure.
- Factors Affecting Material Costs:
- Material Type: Engineering plastics like PEEK or polycarbonate tend to be more expensive than commodity plastics like HDPE or PP.
- Material Quantity: Larger production runs can reduce the cost per unit of material, but small batches may result in higher material costs per part.
- Material Quality: Higher-grade or specialized materials may increase the cost due to their enhanced properties (e.g., durability, heat resistance, or aesthetic appeal).
3. Machine Usage and Maintenance:
The type of injection molding machine used and its maintenance also impact costs. Machines vary by size, speed, and technology, and each comes with associated operating costs, including energy consumption, maintenance, and depreciation.
- Factors Affecting Machine Costs:
- Machine Type: Injection molding machines come in various types: hydraulic, electric, and hybrid. Electric machines tend to be more energy-efficient but may have a higher upfront cost.
- Cycle Time: The faster the cycle time, the more parts can be produced per hour, reducing the per-unit cost. However, achieving shorter cycle times may require optimizing machine settings or upgrading equipment.
- Machine Maintenance: Ongoing maintenance and repairs of the machine can add up, particularly for high-precision machines that require frequent adjustments.
4. Cycle Time and Labor:
Cycle time refers to the time it takes to complete one cycle of injection, cooling, and ejection of a part. Shorter cycle times result in more parts produced per hour, but longer cycle times are sometimes necessary for larger or more complex parts. Labor costs, including machine operators and quality inspectors, are also tied to cycle time.
- Factors Affecting Cycle Time Costs:
- Part Complexity: More complex parts with thicker walls or more intricate designs may require longer cooling and solidification times.
- Automation: Automated systems can reduce labor costs, but the initial investment in robotics and automated inspection can be high.
How to Reduce Plastic Injection Molding Costs
Reducing the costs associated with plastic injection molding is essential for maximizing profitability while maintaining quality. Here are several strategies for optimizing production to cut costs:
1. Optimize Mold Design and Efficiency:
A well-designed mold can significantly reduce production costs. By focusing on simplifying part designs and improving mold efficiency, manufacturers can reduce the frequency of repairs and maintenance, leading to fewer machine downtimes and longer mold life.
- Strategies:
- Design for Manufacturability (DFM): Simplify part designs to avoid unnecessary complexity and reduce mold costs. This might involve reducing the number of undercuts, cores, or detailed features that require special tooling.
- Multi-Cavity Molds: Using multi-cavity molds allows for the production of multiple parts per cycle, lowering the cost per unit. A well-balanced multi-cavity mold ensures efficient material distribution and even cooling.
- Modular Molds: Modular molds can be customized with interchangeable inserts, allowing manufacturers to produce a variety of parts using the same mold framework. This reduces mold costs for producing different designs.
2. Choose the Right Material:
Material selection directly impacts both upfront costs and production efficiency. While high-performance materials may be necessary for certain applications, choosing a cost-effective material without sacrificing quality can greatly reduce costs.
- Strategies:
- Material Substitution: Consider using lower-cost materials that still meet the product’s performance requirements. For example, switching from an engineering plastic like polycarbonate to a commodity plastic like polypropylene could reduce costs significantly.
- Bulk Purchasing: Ordering materials in larger quantities can reduce the cost per unit of raw material, especially if consistent production runs are planned.
3. Reduce Cycle Times:
One of the most effective ways to reduce costs is by shortening the cycle time, which increases the number of parts produced per hour. A faster cycle time means the injection molding machine can operate more efficiently, reducing the per-unit cost.
- Strategies:
- Optimize Cooling Time: Faster cooling systems or temperature control technologies can reduce the cooling time, speeding up the cycle. This may include using higher-performance cooling channels or materials that cool more quickly.
- Use Hot Runner Systems: Hot runner molds eliminate the need for cooling of the runner system, reducing material waste and cycle time. This can also improve part quality by maintaining a consistent melt temperature.
4. Leverage Automation and Robotics:
Automation plays a crucial role in improving efficiency and reducing labor costs. Automated systems can handle tasks such as part ejection, inspection, and even material loading, reducing the need for manual labor and speeding up production.
- Strategies:
- Automated Part Handling: Implement robots or automated systems for part handling to reduce cycle times and labor costs.
- Automated Inspection: Use automated inspection systems to quickly detect defects, ensuring that only high-quality parts are sent to the next stage of production.
5. Regular Machine Maintenance:
Preventative maintenance ensures that the injection molding machine operates at peak efficiency. A well-maintained machine reduces the risk of breakdowns, which can lead to expensive repairs and production delays.
- Strategies:
- Scheduled Maintenance: Regularly check and maintain machines to ensure proper functioning, focusing on key areas like hydraulic systems, clamping units, and temperature controls.
- Upgrade to Energy-Efficient Machines: Invest in machines that offer energy efficiency or lower operating costs, like electric injection molding machines, which reduce energy consumption compared to traditional hydraulic machines.
6. Design for Cost Efficiency:
Designing parts with cost-efficient manufacturing in mind is one of the most effective ways to reduce overall injection molding costs. This approach focuses on creating designs that are easier to produce and require fewer resources.
- Strategies:
- Reduce Part Weight: Lighter parts require less material, which can lower material costs and reduce the cooling time.
- Minimize Wall Thickness: Reducing the thickness of the walls can lower material usage and shorten the cycle time. However, be cautious of warping or other quality issues when making adjustments.
By implementing these strategies, manufacturers can reduce the overall cost of plastic injection molding while still maintaining the quality, precision, and efficiency required for high-performance applications. Optimizing mold design, material selection, cycle times, and automation are all essential for lowering costs and improving profitability.
Cost Factors in Plastic Injection Molding
Breakdown of Injection Molding Costs
Plastic injection molding is a widely used manufacturing process due to its efficiency in producing high-volume parts. However, several factors influence the overall cost of production. Understanding these cost factors can help manufacturers streamline their processes and make more informed decisions to maximize profitability. Here’s a breakdown of the main elements that contribute to the cost of injection molding:
1. Mold Design and Fabrication Costs:
The mold is a critical part of the injection molding process, and the complexity of its design directly impacts production costs. Mold fabrication involves designing and creating custom molds that will shape the plastic into the final product. These molds are typically made from high-quality materials such as steel or aluminum, with steel offering greater durability but a higher cost.
- Key Factors Affecting Mold Costs:
- Design Complexity: More complex designs that require intricate details, multiple cavities, or unique features (e.g., undercuts or cores) will result in higher mold costs.
- Material of the Mold: Steel molds are more expensive but last longer and are better for high-volume runs, while aluminum molds are more affordable but tend to wear out faster.
- Size and Weight of Mold: Larger molds require more material and longer production time, adding to the cost.
2. Material Choice:
The type of material selected for the injection molding process greatly impacts both the material costs and the overall quality of the final product. Common materials include thermoplastics (like ABS, polystyrene, polypropylene) and engineering plastics (such as nylon, polycarbonate, PEEK). Each material has its own cost structure, and the price can vary based on the quantity required and its suitability for the specific application.
- Factors Affecting Material Costs:
- Material Type: Specialty materials like high-performance polymers or bio-based plastics tend to cost more than standard plastics.
- Material Volume: The more material used per cycle, the higher the cost. For small or complex parts, material usage can be minimized, but for larger components, material costs are higher.
- Waste Reduction: Waste material, particularly in multi-cavity molds or when dealing with runners and sprues, can increase material costs if not efficiently reused.
3. Machine Usage and Operational Costs:
The type of injection molding machine and its operational efficiency are major factors in determining the overall cost. Machines vary in terms of size, speed, and technology, and these differences can significantly impact energy usage and machine life. Hydraulic machines, for example, tend to consume more energy than electric machines, though they can be more cost-effective for certain applications.
- Factors Affecting Machine Costs:
- Machine Type: Hydraulic machines are typically more affordable but less energy-efficient than electric machines, which are more precise and energy-efficient.
- Machine Size and Clamping Force: Larger machines with greater clamping force are needed for larger parts, which can increase machine costs, but they are essential for producing bigger, more complex parts.
- Cycle Time: The longer the cycle time, the more the machine operates, leading to higher energy and labor costs.
4. Cycle Time:
Cycle time refers to the amount of time it takes to complete one full cycle of injection molding, which includes injection, cooling, and ejection. The cycle time is influenced by the complexity of the part, the size of the mold, and the material used. Reducing cycle time can significantly decrease the overall cost per unit.
- Factors Affecting Cycle Time Costs:
- Part Complexity: More complex parts with thicker walls or intricate features require longer cooling times, which increases cycle time and cost.
- Mold Design: Efficient mold design, including optimized cooling channels and part geometries, can reduce cycle time and overall cost.
- Cooling Efficiency: Improving cooling systems, such as using hot runner molds or optimizing the cooling channels, can reduce cooling times and speed up the overall cycle.
How to Reduce Plastic Injection Molding Costs
Reducing the costs associated with plastic injection molding is a critical goal for manufacturers who want to remain competitive in the market. Here are some effective strategies for optimizing production and cutting costs:
1. Optimize Mold Design and Efficiency:
Investing time and effort into designing molds that are efficient and cost-effective can significantly lower overall production costs. A well-designed mold minimizes maintenance and can lead to a longer mold life, which helps spread the mold cost over many production cycles.
- Strategies to Reduce Mold Costs:
- Design for Manufacturability (DFM): Simplify part designs to reduce mold complexity. Avoid unnecessary undercuts, cores, and features that require special tooling. Using standard mold designs and components can reduce both time and cost.
- Multi-Cavity Molds: Utilizing multi-cavity molds allows multiple parts to be produced in a single cycle, reducing the cost per unit.
- Modular Molds: Modular molds, where components can be swapped out for different parts, allow manufacturers to produce multiple parts using the same base mold, reducing overall mold costs.
2. Select Cost-Effective Materials:
Material choice plays a significant role in the cost of injection molding. While high-performance materials are sometimes necessary for certain applications, more cost-effective materials should be used when possible. Additionally, sourcing materials in bulk can help reduce material costs.
- Strategies to Reduce Material Costs:
- Use Commodity Plastics: If performance specifications allow, consider using commodity plastics like polypropylene or HDPE, which are generally cheaper than engineering plastics.
- Buy in Bulk: Purchasing materials in larger quantities can often result in lower per-unit costs. Additionally, negotiating with suppliers for bulk discounts can lead to savings over time.
- Recycling Material: Where possible, use recycled material or reduce material waste by optimizing part design and reusing scrap material (such as runners and sprues) to minimize costs.
3. Reduce Cycle Time:
Shortening cycle times is one of the most effective ways to lower per-unit costs. The quicker the cycle, the more parts can be produced in a given period, which reduces the cost per part.
- Strategies to Reduce Cycle Times:
- Improve Cooling Systems: One of the most significant time savings comes from optimizing the cooling process. Faster cooling times can be achieved by redesigning molds to incorporate more efficient cooling channels.
- Use Hot Runner Molds: Hot runner systems maintain the temperature of the plastic during injection and eliminate the need to cool and eject the runner, reducing cycle time.
- Optimize Injection Speed: Adjusting injection speeds and pressures to the specific material being used can reduce cycle time without compromising part quality.
4. Invest in Automation:
Automating certain aspects of the injection molding process can save time, reduce labor costs, and improve precision. Automation can be applied in various areas, from part ejection to material handling and quality control.
- Strategies for Automation:
- Automated Part Handling: Use robots or automated systems for part ejection, assembly, and packaging. Automation can reduce labor costs, increase speed, and minimize human error.
- Automated Quality Control: Implement automated inspection systems that use cameras or sensors to detect defects and ensure high-quality standards are maintained throughout the production process.
5. Machine Maintenance and Calibration:
Regular machine maintenance ensures that equipment is running at peak efficiency, which can reduce downtime and avoid costly repairs.
- Strategies for Reducing Machine-Related Costs:
- Preventative Maintenance: Schedule regular maintenance to ensure that machines are running smoothly and to avoid unexpected breakdowns that can halt production.
- Energy-Efficient Machines: Consider upgrading to more energy-efficient machines, such as electric machines, which consume less energy and have lower operational costs than hydraulic models.
By optimizing mold design, material selection, cycle time, and automation, manufacturers can significantly reduce the cost of plastic injection molding while maintaining high product quality. These strategies not only help cut costs but also increase overall efficiency and competitiveness in the market.
Sustainable Plastic Injection Molding
As environmental concerns grow, many industries, including plastic injection molding, are increasingly focused on adopting sustainable practices. The shift towards more eco-friendly manufacturing methods not only helps reduce environmental impact but also offers significant benefits in terms of cost savings, regulatory compliance, and consumer appeal. Here’s how sustainable plastic injection molding is making a difference in the industry.
Eco-Friendly Practices in Injection Molding
The demand for more sustainable manufacturing processes has led to several eco-friendly practices gaining traction in the plastic injection molding industry. Manufacturers are now focused on reducing their carbon footprint by incorporating sustainable materials, optimizing energy usage, and minimizing waste.
1. Use of Sustainable Materials:
One of the most significant shifts in plastic injection molding has been the move towards using sustainable materials. These include biodegradable plastics, bio-based plastics made from renewable resources (like PLA or PHA), and recycled plastics.
- Biodegradable Plastics: Bioplastics such as polylactic acid (PLA) or polyhydroxyalkanoates (PHA) are derived from renewable sources like corn starch or plant sugars. While they offer environmental benefits, their use in injection molding is limited by material properties and cost.
- Recycled Plastics: Using recycled plastics reduces the demand for virgin materials, which helps reduce resource extraction and lowers the overall environmental impact. Recycled materials such as recycled polyethylene (rPE) and recycled polypropylene (rPP) are increasingly being used in the injection molding process.
- Sustainable Sourcing: Manufacturers are also exploring sustainable sourcing for their raw materials, ensuring that the production processes adhere to ethical and eco-friendly standards.
2. Energy-Efficient Injection Molding Machines:
Energy consumption is a significant factor in the environmental footprint of injection molding. To reduce energy usage, manufacturers are switching to more energy-efficient injection molding machines, such as electric injection molding machines, which consume less power compared to traditional hydraulic machines.
- Electric Machines: Electric machines offer precise control and higher energy efficiency. They typically consume 30–50% less energy than hydraulic machines because they only draw power when required, unlike hydraulic machines, which use constant energy to operate.
- Optimization of Machine Settings: By fine-tuning injection pressures, temperatures, and cycle times, manufacturers can reduce energy consumption during production. Some machines are even designed with energy-saving modes, which further improve efficiency.
3. Efficient Mold Design:
The efficiency of mold design plays a crucial role in minimizing waste and energy use. Improved mold designs not only reduce production costs but also minimize material waste and energy consumption.
- Conformal Cooling: Advances in mold design, such as conformal cooling channels, improve cooling efficiency. This reduces cycle times, saving energy and reducing the environmental impact.
- Tooling for Multiple Products: Designing molds with multiple cavities or using modular tooling systems allows manufacturers to produce several parts in a single cycle, maximizing the efficiency of each production run.
Recycling and Reusing Plastic in Injection Molding
Recycling and reusing plastic materials in injection molding are two critical strategies that help mitigate the environmental impact of plastic production. By adopting recycling practices, manufacturers can reduce waste, conserve resources, and lower costs.
1. Recycling Scrap Plastic:
Plastic scrap generated during the injection molding process, such as runners, sprues, and defective parts, often ends up as waste. However, with the right recycling practices in place, this plastic can be reused in future production runs, reducing material waste and conserving resources.
- Grinding and Reprocessing: Scrap plastic can be ground down and reprocessed to create new pellets, which can then be injected into the mold. This process reduces the need for virgin plastic and helps lower overall material costs.
- Closed-Loop Recycling: In closed-loop recycling, scrap from production is directly recycled into the same type of product. This process ensures that the plastic remains within the same material cycle, which is beneficial for reducing waste and minimizing resource extraction.
2. Use of Recycled Materials:
In addition to recycling scrap plastic, manufacturers are increasingly using post-consumer recycled (PCR) materials in their injection molding processes. These materials, which are collected from consumer products like bottles, containers, and packaging, are cleaned, sorted, and processed for use in manufacturing new parts.
- Post-Consumer Recycled Plastics: Using recycled materials not only reduces waste but also lessens the environmental burden of producing virgin plastics. Recycled plastics like rPET (recycled polyethylene terephthalate) and rHDPE (recycled high-density polyethylene) are commonly used in injection molding, especially for packaging and consumer products.
- Recycled Content Standards: To ensure the quality of recycled materials, manufacturers often follow established standards such as the ISO 14021 for recycled content, ensuring that the material used meets the required performance and durability levels.
3. Reducing Plastic Waste Through Efficient Production:
Efficient production practices play a critical role in reducing plastic waste. By optimizing injection molding processes, manufacturers can minimize scrap and defects.
- Optimizing Mold Design for Minimal Waste: Advanced mold designs that reduce the number of defects or unnecessary parts can minimize waste. For instance, using efficient gating systems can prevent excessive plastic use and reduce the amount of scrap generated.
- Process Monitoring: Regular monitoring of production processes helps identify areas where waste can be reduced. Automated systems can also help detect and correct issues before they result in excessive scrap material.
4. Repurposing Used Parts:
Another aspect of sustainable injection molding is repurposing parts that are no longer needed in their original form. These parts can be disassembled, reprocessed, and remade into new products, further extending the lifecycle of the material.
- Remanufacturing: Remanufacturing used plastic parts into new components is another form of recycling that can be beneficial. For example, plastic components from old electronics or appliances can be melted down and reformed into new parts, giving the materials a second life.
By incorporating both recycling and reusing practices into the injection molding process, manufacturers can reduce the environmental impact of their operations. Sustainable injection molding not only addresses the growing demand for eco-friendly production but also aligns with the industry’s broader efforts toward circular economies, where products and materials are reused, refurbished, and recycled to reduce waste and conserve resources. This shift not only benefits the environment but also offers long-term cost savings and improved efficiency for manufacturers.
Future Trends in Plastic Injection Molding
Plastic injection molding continues to evolve, driven by technological innovations and shifting market demands. As the industry moves forward, we’re seeing significant transformations powered by automation, robotics, and the integration of new materials and techniques. These advancements promise to make plastic injection molding more efficient, precise, and sustainable, opening up new possibilities for manufacturers across industries.
Automation and the Future of Injection Molding
In the coming years, automation will play an even more significant role in shaping the injection molding landscape. The integration of robotics, AI, and machine learning is enhancing efficiency, reducing human error, and improving overall production quality. Here’s a closer look at how automation is changing the industry:
1. Streamlining Production Processes:
The use of robots and automated systems in plastic injection molding is drastically reducing the need for manual labor, particularly for repetitive and precision-based tasks. Robots can handle everything from part removal and packaging to secondary operations like trimming and assembly. By automating these steps, manufacturers are able to cut down on human error, reduce cycle times, and achieve higher output in less time.
- Robotic Arm Integration: Robotic arms are designed to interact with the molding machines, picking up parts directly from the molds, and placing them into packaging or moving them to the next stage of production. This reduces manual labor and speeds up the process significantly.
- Automated Quality Control: With advancements in artificial intelligence and vision systems, automated quality control systems can now identify defects and irregularities during production. This enables real-time feedback and adjustments, reducing defects and improving product consistency.
2. Enhanced Precision and Consistency:
Automated systems allow for fine-tuning of machine settings and real-time adjustments during the production process. This leads to higher precision and consistency across every part that comes off the production line.
- Machine Learning for Process Optimization: Machine learning algorithms can analyze data from previous molding cycles to identify optimal settings and improve production efficiency. For example, it can predict when a machine is likely to experience wear or malfunction, allowing for preventive maintenance, which reduces downtime and keeps the production running smoothly.
3. Decreasing Human Error and Improving Safety:
By incorporating automation into production, the injection molding process becomes less reliant on human intervention, reducing the likelihood of errors caused by fatigue, distractions, or poor handling. This not only improves the quality of the end product but also increases workplace safety, particularly in high-risk operations.
4. Industry 4.0 and Smart Factories:
As more manufacturers adopt smart technologies and interconnected systems, the injection molding industry is transitioning into Industry 4.0. In a smart factory environment, machines, robots, and sensors are all linked, allowing for real-time monitoring of production conditions. This data is analyzed to optimize manufacturing processes and predict potential issues before they arise.
- Predictive Maintenance: Sensors embedded in machines can monitor operational parameters like temperature, pressure, and vibration, alerting technicians to potential issues before they lead to costly breakdowns. This predictive maintenance helps to prolong the life of machines and reduce downtime, ensuring higher efficiency in the production process.
Innovations in Plastic Injection Molding Technology
The injection molding process is undergoing significant technological advancements that are expanding the capabilities of manufacturers. The integration of cutting-edge techniques like 3D printing, smart molds, and advanced materials is transforming the way products are designed and manufactured.
1. 3D Printing and Injection Molding Integration:
While 3D printing and injection molding are often seen as separate technologies, their combination is set to change the manufacturing landscape. 3D printing can be used to create prototypes quickly, while injection molding can produce parts in high volumes. The two technologies can complement each other in several ways:
- Rapid Prototyping: With 3D printing, manufacturers can quickly create prototypes of molded parts to test designs, ensuring that they meet specifications before committing to the cost of traditional tooling and molds. This accelerates the product development cycle and reduces costs associated with trial and error.
- Customization of Molds and Inserts: 3D printing allows for the creation of custom mold inserts or core components that would be difficult or time-consuming to manufacture using conventional methods. This can lead to more complex, cost-effective molds that enhance the capabilities of injection molding.
2. Smart Molds and Sensors:
Smart molds equipped with sensors are revolutionizing the injection molding process. These molds can provide real-time feedback about key factors such as pressure, temperature, and flow rates, enabling manufacturers to monitor and adjust the molding process on the fly.
- Real-Time Monitoring: By embedding sensors into molds, manufacturers can collect critical data about the molding process as it occurs. This data can be analyzed to ensure that each part is produced to the correct specifications, which helps to prevent defects and ensures consistent quality.
- Adaptive Mold Technology: Some smart molds have the capability to make adjustments during the molding process. For instance, if a mold’s temperature deviates from an ideal range, it can automatically adjust to optimize cooling rates and avoid defects such as warping or sink marks.
3. Advanced Materials and Nanotechnology:
The development of advanced materials, including nanomaterials, is opening up new opportunities for plastic injection molding. Materials with enhanced properties, such as increased strength, flexibility, and heat resistance, are being incorporated into molded parts to meet the demands of industries like aerospace, automotive, and electronics.
- Nano-Enhanced Plastics: Nanotechnology is enabling the production of plastics with improved mechanical and electrical properties. These advanced materials can be used to produce parts with higher strength-to-weight ratios, better conductivity, and improved resistance to wear and tear.
- Lightweight Materials: Innovations in lightweight materials, such as carbon fiber composites and glass-fiber-reinforced plastics, are increasingly used in injection molding, especially for applications in the automotive and aerospace industries. These materials offer the strength of metals without the added weight, leading to more fuel-efficient vehicles and aircraft.
4. Bioplastics and Sustainable Materials:
As sustainability becomes a major focus for industries worldwide, bioplastics and other environmentally friendly materials are gaining traction in the injection molding process. These materials, derived from renewable sources like plant-based resins, offer an eco-friendly alternative to traditional petroleum-based plastics.
- Biodegradable Plastics: Advances in biodegradable plastics are allowing manufacturers to reduce their environmental impact. These plastics break down naturally over time, minimizing long-term pollution and waste.
- Recycling and Circular Economy: The future of injection molding will increasingly involve the use of recycled materials. Manufacturers are developing new ways to recycle scrap plastic and incorporate it back into the production process, further reducing waste and promoting sustainability.
The future of plastic injection molding is shaped by the growing role of automation, innovative technologies, and sustainable practices. Automation and robotics are enhancing efficiency and precision, while new advancements in 3D printing, smart molds, and advanced materials are pushing the boundaries of what can be achieved. As these trends continue to evolve, plastic injection molding will become more efficient, versatile, and environmentally friendly, driving the industry toward a new era of manufacturing excellence.
Conclusion
Plastic injection molding has firmly established itself as one of the most efficient, precise, and versatile manufacturing processes available today. From its ability to produce high volumes of consistent, intricate parts to its compatibility with a wide range of materials, injection molding continues to offer businesses across industries a host of compelling advantages.
Key Benefits:
- Efficiency: Injection molding is one of the fastest manufacturing methods, particularly when it comes to large-scale production. Its ability to produce thousands of parts in a short time frame makes it ideal for high-volume manufacturing needs, reducing both time and labor costs.
- Precision: The process is known for its remarkable accuracy, allowing businesses to produce parts with complex geometries and tight tolerances. This precision is especially important in industries like automotive, medical devices, and electronics, where even the smallest defect can have significant consequences.
- Versatility: Whether you need to produce plastic components in a range of shapes, sizes, or materials, injection molding provides the flexibility to meet diverse design requirements. With options like multi-material molding and the use of advanced materials such as bioplastics, manufacturers can meet a broad array of functional, aesthetic, and environmental needs.

Why Choose Injection Molding?
For businesses looking to streamline production, reduce waste, and ensure product consistency, plastic injection molding is a highly viable and scalable option. Its ability to meet high demand, produce high-quality products, and accommodate complex designs makes it an indispensable tool for companies aiming for excellence in manufacturing.
Whether you’re in the automotive, medical, consumer goods, or electronics sector, injection molding can provide you with the cost efficiency, flexibility, and precision you need to stay competitive in today’s fast-paced market. By choosing injection molding, you’re not only investing in a production method, you’re securing the long-term sustainability and growth of your business.
If you’re considering ways to optimize your manufacturing processes or looking to scale your production, plastic injection molding should undoubtedly be at the top of your list. Reach out to an experienced injection molding provider and explore how this process can help take your business to the next level.
FAQ
10. Can injection molding be used for small production runs?
Injection molding is typically more cost-effective for large-scale production due to high initial mold costs. However, it is still possible to produce smaller quantities using low-volume molding techniques or by modifying the design of the mold to reduce costs.
11. What is a “smart mold” in injection molding?
A “smart mold” refers to molds that incorporate sensors and advanced technology to monitor parameters like temperature, pressure, and material flow during the injection molding process. These molds can automatically adjust to optimize the molding process and reduce defects.
13. Can injection molding be used for multi-material or color parts?
Yes, injection molding can produce multi-material or multi-color parts using techniques like overmolding or two-shot molding. This allows for the combination of different materials or colors in a single, complex part without the need for additional assembly.