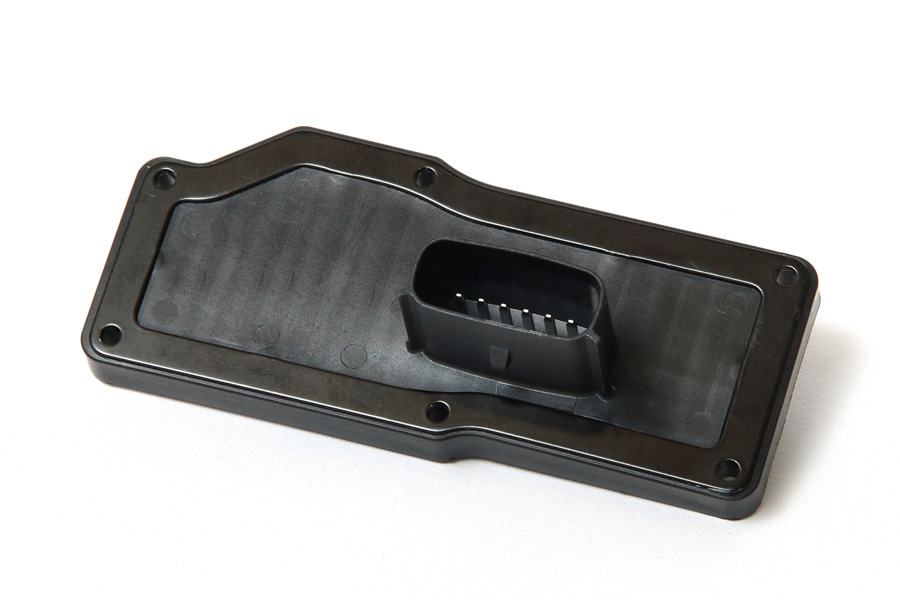
Your blog feed for digital manufacturing resources, in-depth features, and industry news.
Whether you need standard storage buckets or specialized containers for specific industries, plastic injection molding offers unmatched efficiency, precision, and scalability.
In this article, we’ll explore why plastic injection molding is the ideal method for producing high-quality plastic buckets and how it can benefit your business.
Plastic injection molding is a process where melted plastic is injected into a mold cavity under high pressure. The plastic then cools and solidifies, taking the shape of the mold. This process is used to create a wide range of products, from everyday household items to complex industrial components.
For plastic buckets, the process involves injecting plastic material into molds specifically designed for bucket shapes. These molds can be customized to produce different sizes, designs, and features such as handles, lids, and embossed logos.
One of the main reasons businesses choose plastic injection molding for bucket production is its cost-effectiveness for mass production. Once a mold is created, it can produce large quantities of buckets in a short period, making it ideal for high-volume production. The initial cost of the mold may be higher, but the cost per unit decreases as production volumes increase, providing excellent return on investment over time.
Plastic injection molding ensures that each bucket is made to the same specifications with high precision. Whether you need large or small buckets, the molding process ensures consistency in size, shape, and quality. This precision is especially important for buckets that need to fit specific accessories, lids, or machinery.
With injection molding, you can design custom buckets with unique shapes, sizes, or features that cater to specific needs. Whether you need buckets with special handles, reinforced walls, or integrated labels, the flexibility of injection molding allows you to create the exact product your business requires. Custom molds can be created to match your exact specifications, giving you complete control over the final design.
Buckets produced through plastic injection molding are highly durable. The process allows for the use of various types of plastic, such as polypropylene (PP) or polyethylene (PE), which are known for their strength and resistance to wear. These materials ensure that the buckets can withstand heavy-duty usage, harsh chemicals, and various environmental conditions, making them ideal for both industrial and consumer applications.
Once the mold is created, plastic injection molding is a highly efficient process. It can produce hundreds or even thousands of buckets in a single day, making it ideal for businesses that need large quantities of products in a short time. The automation of the injection molding process also reduces human error, leading to fewer defects and quicker turnaround times.
Plastic injection molding is known for its efficiency when it comes to material usage. The process is designed to minimize waste, as the plastic is injected precisely into the mold and any excess material can often be recycled. This means that the overall production process is more environmentally friendly and cost-effective.
Injection molding allows you to integrate custom features into your buckets, such as embossed logos, specific color choices, and specialized patterns. If branding is important to your business, you can easily incorporate your company’s identity into the product. Customization helps create a unique product that stands out in the market.
Plastic buckets manufactured using injection molding are used across a wide range of industries, including:
Mold Design and Complexity The design of the mold will influence both the cost and the quality of the final product. More complex designs, such as buckets with unique features or intricate shapes, may require more time and investment. It’s important to work closely with your mold supplier to ensure that the design meets your specifications.
Material Selection The material you choose for your buckets will depend on the intended use. Common plastics for buckets include polypropylene (PP) and high-density polyethylene (HDPE), which offer durability, flexibility, and resistance to chemicals. It’s essential to choose the right material to meet the performance requirements of your product.
Production Volume Plastic injection molding is most cost-effective for large-scale production. For smaller quantities, the upfront investment in mold creation may not be as cost-efficient. However, as your production volume increases, the cost per unit decreases significantly.
Lead Time The time required to develop the mold and start production can vary. If you have tight timelines, it’s important to discuss the lead time with the manufacturer and ensure that the molding process fits within your production schedule.
Plastic injection molding is a highly efficient and cost-effective manufacturing process for producing plastic buckets in large volumes. The ability to customize designs, ensure precision, and achieve durability makes it the ideal choice for businesses looking to produce high-quality buckets for various industries.
Whether you’re producing standard buckets for industrial use or creating custom buckets with specific features, plastic injection molding provides the flexibility, speed, and consistency needed to meet your business demands. By choosing the right mold and materials, you can ensure that your buckets meet both functional and aesthetic requirements while maximizing your production efficiency.
Investing in plastic injection molding for your bucket production can help your business stay competitive and meet the growing demands of your customers.
Your blog feed for digital manufacturing resources, in-depth features, and industry news.
31 Southlands Road
POLESWORTH
B78 0FL
We will reply to you in 20 minutes.
Our team is online, can be helpful for you.
Our team is online, can be helpful for you.
Didn’t find what you want? Ask our leader for help directly!