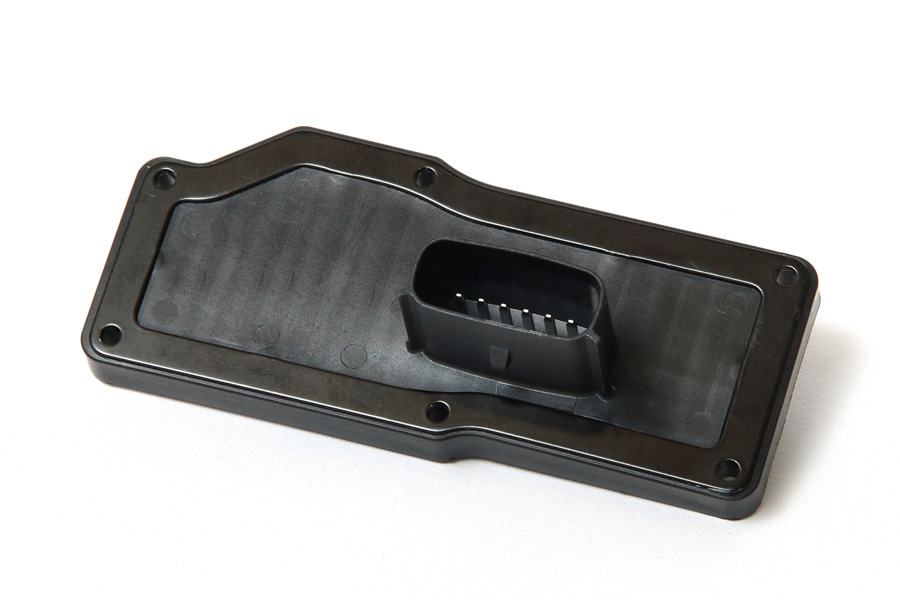
Your blog feed for digital manufacturing resources, in-depth features, and industry news.
The process behind producing these plastic buckets efficiently relies heavily on the quality of the plastic bucket mold.
A plastic bucket mold is a crucial tool in the injection molding process, responsible for shaping the plastic material into the desired form. In this article, we’ll dive into the importance of a good plastic bucket mold, the benefits it offers, and the key factors to consider when selecting one for your production needs.
A plastic bucket mold is a specialized tool used in injection molding to produce plastic buckets. The mold is typically made from durable materials like steel or aluminum and is designed to withstand the high pressures and temperatures of the molding process. Once the mold is created, plastic resin is injected into the cavity, where it solidifies into the shape of a bucket.
Plastic bucket molds can be designed to create a variety of bucket sizes and shapes, with different features such as handles, lids, or embossed logos. The quality and design of the mold play a significant role in the final product’s appearance, strength, and functionality.
A well-designed plastic bucket mold ensures that each bucket produced is identical in shape, size, and quality. This consistency is critical for businesses that need large volumes of the same product, whether for retail distribution or industrial use. A high-quality mold reduces the risk of defects, ensuring a high standard of production.
The durability of a plastic bucket mold directly impacts the longevity and performance of the production line. A mold that is built to last will withstand the constant stress of high-temperature plastic injection and repeated cycles, allowing for continuous production without frequent downtime for mold replacements.
Investing in a high-quality mold may seem like a significant upfront cost, but it can save you money in the long run. A mold that produces high-quality, defect-free buckets with minimal waste leads to more efficient production. Additionally, fewer rejections and repairs translate to lower operational costs over time.
Whether you need standard plastic buckets or customized versions with specific features (such as handles, special shapes, or labels), a good plastic bucket mold can be tailored to meet your requirements. Custom molds allow businesses to produce unique products that stand out in the market, giving them a competitive edge.
A well-designed mold also contributes to shorter cycle times in the injection molding process. This means faster production speeds, allowing you to meet customer demands quickly and efficiently. With optimized molds, you can increase throughput without compromising on product quality.
The material of the mold itself is one of the most important factors. Steel molds are typically more durable and can withstand higher temperatures and pressures, making them ideal for large-scale production. Aluminum molds, on the other hand, are more cost-effective and suitable for smaller production runs or less demanding applications.
The complexity of the mold design depends on the features of the bucket you want to produce. If your bucket requires intricate designs, handles, or embossed logos, you’ll need a more complex mold that can accommodate these features. It’s important to work with mold manufacturers who can create molds that meet your specific design requirements.
The mold you choose should be compatible with the injection molding machines you use. The size and specifications of the mold need to match the capacity of your equipment to ensure a smooth and efficient production process. Always ensure that the mold can integrate seamlessly with your existing machinery.
The efficiency of a plastic bucket mold in terms of production cycle time is crucial for maintaining a smooth production flow. A mold that is designed for quick injection and cooling will improve overall cycle times, allowing for faster turnaround on large orders.
Over time, molds wear down due to constant use, which can lead to issues such as surface defects or dimensional inaccuracies. Choosing a mold that is easy to maintain and repair ensures that your production stays efficient and cost-effective. Some manufacturers offer services to help maintain and refurbish molds, extending their lifespan.
Standard Bucket Molds These molds are designed to produce standard plastic buckets, typically used for storage or packaging. They can be customized for different sizes and thicknesses, depending on the specific needs of the user.
Customized Bucket Molds For unique applications, such as buckets with custom logos, handles, or lids, a customized mold is required. These molds are often more complex and require precise design to achieve the desired result.
Stack Molds Stack molds allow for the production of multiple buckets in a single cycle, improving efficiency and reducing costs. These are particularly useful for high-volume production.
Multi-Cavity Molds These molds allow for the production of several buckets at once, improving production rates. Multi-cavity molds are ideal for large-scale production runs where volume and speed are crucial.
A high-quality plastic bucket mold is an investment that directly impacts the efficiency, quality, and cost-effectiveness of your production process. Whether you’re producing standard buckets or custom designs, choosing the right mold ensures consistent results, reduced operational costs, and faster production times.
When selecting a mold, consider factors such as material durability, mold design, machine compatibility, and cycle time efficiency. Partnering with an experienced mold manufacturer will ensure you get a product that meets your needs and helps your business thrive.
With the right plastic bucket mold, you can produce durable, high-quality buckets that meet the demands of your market, whether for industrial use, consumer products, or specialized applications.
Your blog feed for digital manufacturing resources, in-depth features, and industry news.
31 Southlands Road
POLESWORTH
B78 0FL
We will reply to you in 20 minutes.
Our team is online, can be helpful for you.
Our team is online, can be helpful for you.
Didn’t find what you want? Ask our leader for help directly!