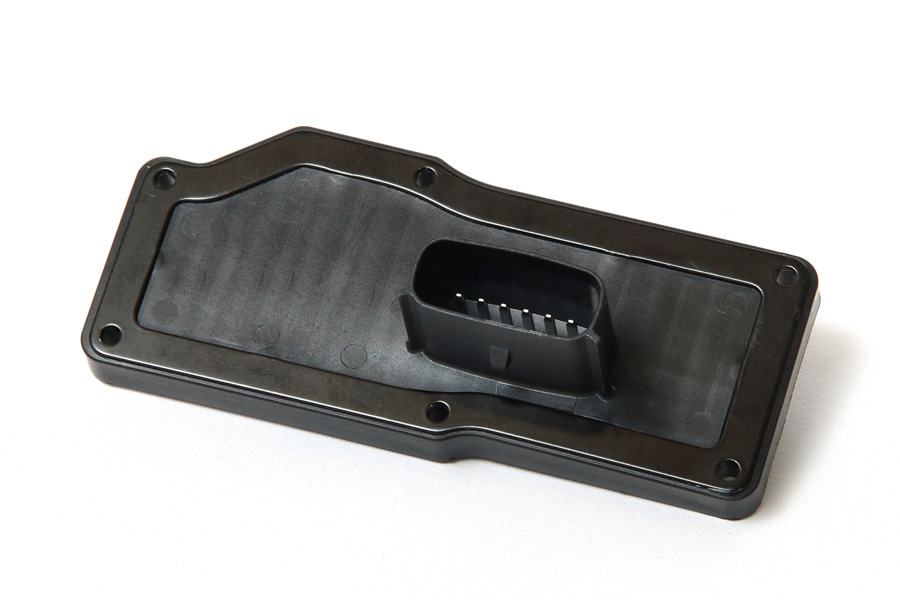
Your blog feed for digital manufacturing resources, in-depth features, and industry news.
As businesses and manufacturers look for more efficient, cost-effective, and environmentally friendly ways to produce plastic buckets, new molding technologies have emerged to meet these demands. In this article, we’ll explore some of the latest innovations in plastic bucket molding that are shaping the industry.
One of the most exciting developments in plastic bucket molding is the use of 3D printing to prototype molds. Traditionally, creating a mold for plastic buckets was a time-consuming and costly process. With 3D printing, manufacturers can now quickly produce prototype molds, allowing for faster design iterations and reducing the time it takes to bring a new bucket design to market.
Benefits:
Automation is revolutionizing the manufacturing process, and plastic bucket molding is no exception. New technologies have enabled automated mold production systems that reduce the need for manual labor, improve precision, and increase production efficiency.
Benefits:
As energy costs rise and environmental concerns grow, manufacturers are increasingly turning to energy-efficient molding techniques to reduce their carbon footprint and lower operational costs. Techniques such as low-pressure injection molding and energy-saving hydraulic systems are becoming more popular in plastic bucket manufacturing.
Benefits:
The choice of materials used in plastic bucket production has also evolved. Advanced polymers are now being used to enhance the durability, strength, and flexibility of plastic buckets. Materials like high-density polyethylene (HDPE) and reinforced polypropylene (PP) are popular choices for producing robust and long-lasting buckets.
Benefits:
Multilayer molding involves using two or more layers of different materials during the molding process. This technique is gaining popularity in plastic bucket manufacturing because it improves the performance and aesthetics of the final product. For example, a plastic bucket can have a strong outer layer for durability and a softer, more flexible inner layer to prevent cracking.
Benefits:
The ability to quickly switch molds for different designs is an important innovation in the plastic bucket molding process. Quick-change molds allow manufacturers to easily adapt their production lines for different bucket designs, improving flexibility and reducing downtime between production runs.
Benefits:
Sustainability is a growing concern in the manufacturing industry, and plastic bucket molding is embracing more eco-friendly practices. Innovations such as biodegradable plastics, recycled materials, and closed-loop systems are becoming increasingly popular in the production of plastic buckets.
Benefits:
The plastic bucket molding industry has seen remarkable advancements in recent years, with innovations that improve efficiency, sustainability, and product quality. From 3D printing for mold prototyping to energy-efficient molding techniques and the use of advanced materials, manufacturers are pushing the boundaries of what’s possible.
These innovations not only help businesses stay competitive by improving their production processes but also ensure that the final plastic buckets meet the demands of modern consumers. By embracing the latest technologies, manufacturers can produce higher-quality products, reduce costs, and contribute to a more sustainable future.
Your blog feed for digital manufacturing resources, in-depth features, and industry news.
31 Southlands Road
POLESWORTH
B78 0FL
We will reply to you in 20 minutes.
Our team is online, can be helpful for you.
Our team is online, can be helpful for you.
Didn’t find what you want? Ask our leader for help directly!