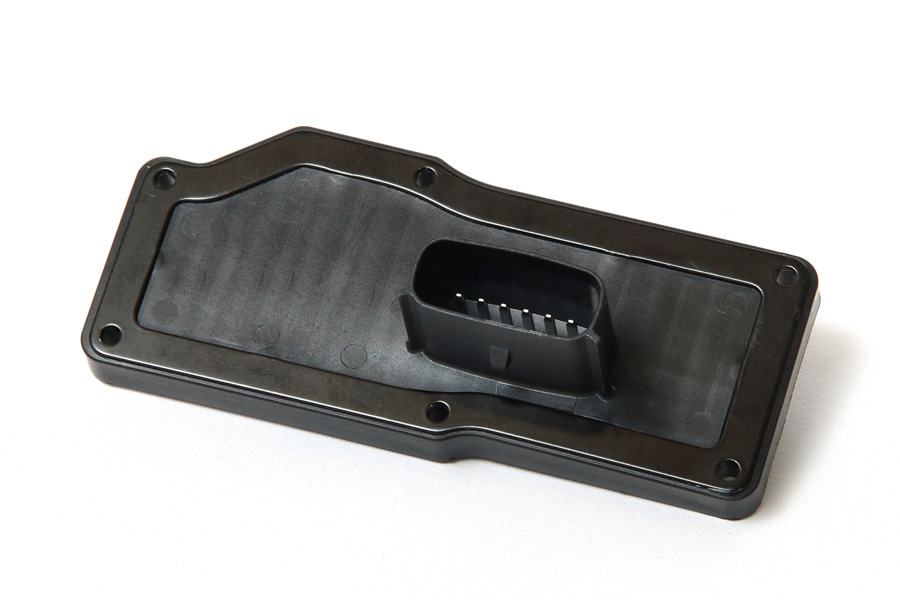
Your blog feed for digital manufacturing resources, in-depth features, and industry news.
Whether in manufacturing, logistics, or mining, conveyors are integral to maintaining smooth operations. However, to ensure these systems run at optimal speed and torque, a speed reducer is a critical component.
In this article, we will explore how speed reducers improve the performance of conveyor systems, why they are necessary, and how selecting the right one can lead to greater efficiency, reliability, and cost savings.
A speed reducer is a mechanical device that reduces the speed of a motor’s output while increasing the output torque. This ensures that the conveyor system operates smoothly and efficiently without overloading the motor. Speed reducers are used in various systems, but in conveyor applications, they are especially vital for managing the load, maintaining speed control, and ensuring precise movements.
Speed reducers are available in various types, including worm gears, planetary gears, and helical gears, depending on the requirements of the application. Each type offers different benefits such as higher efficiency, smoother operation, and better torque control.
Conveyor systems often carry heavy loads and need to move at specific speeds to ensure materials are transported without damage or delays. Here’s why speed reducers are essential for these systems:
Optimal Torque Management A conveyor system may need to move large or heavy materials, which requires more torque. Speed reducers increase the torque from the motor, allowing the conveyor belt to handle heavy loads without straining the motor. This results in a smoother operation and reduces the risk of motor burnout.
Energy Efficiency Speed reducers help reduce the motor’s workload by lowering its speed while maintaining the necessary torque. This makes the conveyor system more energy-efficient, which is especially important in high-volume or continuous processes. By using less energy, businesses can cut operating costs and improve overall system efficiency.
Precise Speed Control Conveyor systems often need to operate at specific speeds to ensure materials are handled correctly. Speed reducers provide the precise speed control necessary for such applications, ensuring that products move at a consistent and optimal speed.
Reduced Wear and Tear Without a speed reducer, the motor would have to work harder to move heavy loads or maintain the desired speed, leading to increased wear and tear. Speed reducers alleviate this strain, extending the life of the motor and other components in the conveyor system.
Improved Safety By ensuring the conveyor runs at the correct speed and torque, speed reducers help prevent sudden jerks or stoppages, which could cause accidents. Consistent operation also reduces the likelihood of mechanical failures that could disrupt operations or cause damage to the conveyor system.
Enhanced Load Handling Speed reducers allow conveyor systems to handle heavier loads without compromising performance. Whether you’re moving bulk materials, heavy packages, or machinery parts, the torque provided by the speed reducer ensures the conveyor operates smoothly even under heavy load conditions.
Reduced Energy Consumption A well-chosen speed reducer reduces the motor’s workload, meaning less energy is needed to move materials along the conveyor. Over time, this leads to significant energy savings and lower electricity bills for businesses that rely heavily on conveyor systems for operations.
Longer Equipment Life With reduced strain on the motor, bearings, and other components, the lifespan of the conveyor system is extended. Speed reducers help prevent overloading and overheating, which can lead to premature failure of the motor or drive components.
Smoother Operations Conveyor systems that use speed reducers operate at a more consistent and predictable pace. This improves the overall flow of materials and minimizes disruptions, ensuring that goods are delivered on time and in good condition.
Better Noise and Vibration Control Speed reducers are designed to operate quietly and smoothly, reducing vibrations that could cause mechanical damage over time. In environments where noise reduction is important, such as food production or clean room environments, speed reducers help maintain a quieter, more efficient operation.
Worm Gear Speed Reducers Worm gear reducers are highly efficient and ideal for applications that require a significant reduction in speed. They are known for their compact design and ability to handle high loads with minimal noise. Worm gears also offer high torque output, making them suitable for heavy-duty conveyor applications.
Planetary Gear Reducers Planetary gear reducers are known for their high torque density, efficiency, and compact design. They provide smooth operation, making them ideal for conveyor systems that require precise control and reliable performance over extended periods.
Helical Gear Reducers Helical gear reducers are another popular choice for conveyor systems. These reducers offer quiet operation, high efficiency, and excellent load-handling capabilities. They are commonly used in applications where smooth, continuous operation is essential.
Selecting the correct speed reducer for your conveyor system can make a significant difference in the overall performance, reliability, and cost-effectiveness of your operation. Here are key factors to consider when choosing a speed reducer:
Load Requirements Consider the weight and size of the materials you need to transport. Ensure that the speed reducer can handle the load without overloading the motor.
Speed and Torque Specifications Determine the desired speed and the amount of torque required to move the materials. The right speed reducer will balance these two factors to achieve optimal performance.
Environmental Conditions Think about the operating environment. Will the conveyor system be exposed to extreme temperatures, moisture, or dust? Choose a speed reducer that can withstand these conditions and continue to perform reliably.
Maintenance Requirements Look for a speed reducer that offers easy maintenance. Some reducers require more frequent lubrication or monitoring, while others are designed to run with minimal maintenance.
Efficiency Consider the overall efficiency of the reducer. More efficient speed reducers will help reduce energy costs and improve the overall performance of your conveyor system.
Incorporating a speed reducer into your conveyor system is essential for optimizing performance, handling heavy loads, and reducing energy consumption. Whether you’re running a factory, a warehouse, or a distribution center, the right speed reducer will ensure your conveyor system operates smoothly and efficiently, contributing to improved productivity and lower operational costs.
By choosing a high-quality speed reducer that suits your specific needs, you can enhance the reliability and longevity of your conveyor system, ultimately improving your bottom line.
Your blog feed for digital manufacturing resources, in-depth features, and industry news.
31 Southlands Road
POLESWORTH
B78 0FL
We will reply to you in 20 minutes.
Our team is online, can be helpful for you.
Our team is online, can be helpful for you.
Didn’t find what you want? Ask our leader for help directly!