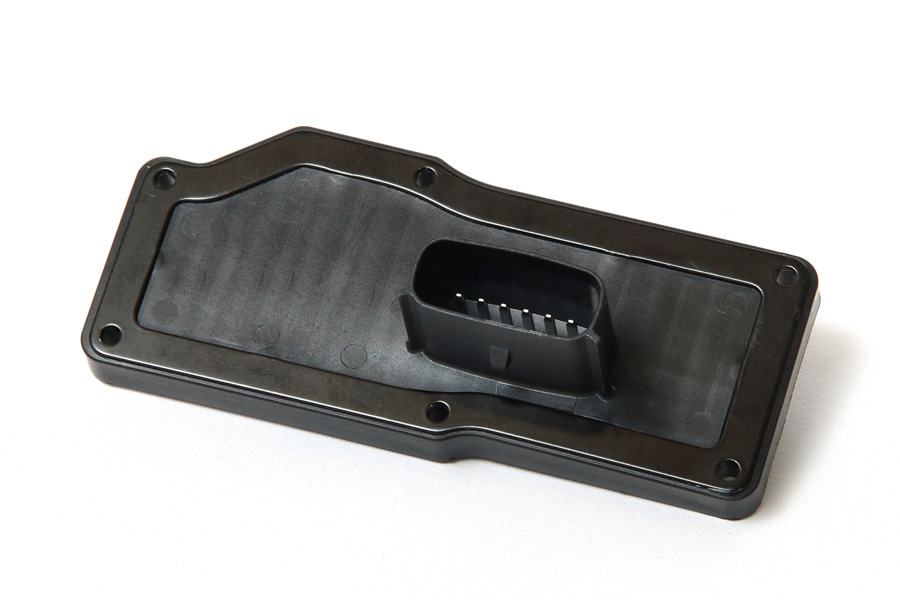
Your blog feed for digital manufacturing resources, in-depth features, and industry news.
The mold is essential for the mass production of plastic buckets, as it ensures consistency and quality in each product. Here’s a simple overview of the process involved in making a plastic bucket mold.
The first step in the process is designing the mold. This involves creating a detailed 3D model or blueprint of the plastic bucket, taking into consideration the desired shape, size, and features. The design will also include the placement of injection points, cooling channels, and venting areas to ensure efficient molding. A clear and accurate design is essential to avoid delays or errors during production.
Once the design is finalized, the next step is choosing the right materials for the mold. Commonly used materials include steel, aluminum, or other alloys, depending on the specific requirements. Steel is often chosen for its durability and ability to withstand repeated use, while aluminum molds are easier to manufacture and are suitable for short runs.
With the materials selected, the fabrication process begins. This involves machining the mold components, including the core, cavity, and mold plates. The core is the part that forms the inside of the bucket, while the cavity forms the outer shape. These components are carefully shaped using precision tools such as CNC machines, ensuring that every detail of the design is replicated accurately.
Once the mold components are fabricated, they are assembled into a complete mold. The mold is then tested to ensure that it meets the required specifications and that the bucket can be molded properly. The testing phase may involve running a sample of the plastic material through the mold to check for issues like air pockets, uneven flow, or defects in the bucket’s shape.
After testing, any necessary adjustments are made to the mold to address issues identified during testing. This may involve tweaking the cooling channels, adjusting the injection points, or refining the mold’s surface to improve the quality of the final product. Once the adjustments are complete, the mold is ready for production.
Once the mold is finalized, it can be used for mass production of plastic buckets. However, regular maintenance is essential to ensure the mold remains in good condition. This includes cleaning the mold, checking for wear and tear, and making necessary repairs or replacements to maintain its efficiency.
The process for making a plastic bucket mold involves careful planning, material selection, fabrication, testing, and adjustments to create a mold that produces high-quality plastic buckets. By ensuring each step is completed with precision, manufacturers can produce consistent and durable plastic buckets that meet the required standards.
Your blog feed for digital manufacturing resources, in-depth features, and industry news.
31 Southlands Road
POLESWORTH
B78 0FL
We will reply to you in 20 minutes.
Our team is online, can be helpful for you.
Our team is online, can be helpful for you.
Didn’t find what you want? Ask our leader for help directly!