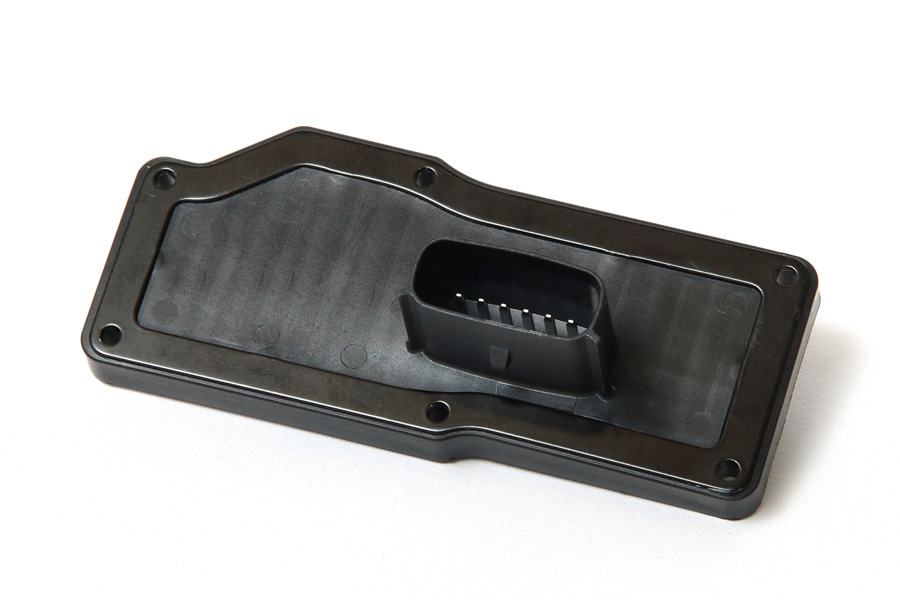
Your blog feed for digital manufacturing resources, in-depth features, and industry news.
Whether you’re dealing with imperfect finishes, dimensional inaccuracies, or production delays, fixing defects promptly is crucial to maintaining efficient production and product quality.
In this article, we’ll explore common defects in plastic bucket molds and provide practical solutions on how to fix them.
Problem: Uneven wall thickness can lead to weak points, warping, and poor durability in plastic buckets. This is often caused by uneven plastic flow, cooling rates, or mold design flaws.
Solution:
Problem: A short shot occurs when the mold doesn’t fill completely, leaving the product incomplete or under-formed. This can happen due to insufficient material or poor injection pressure.
Solution:
Problem: Flashing happens when excess plastic escapes from the mold cavity, creating a thin layer of unwanted material around the edges of the bucket. This often results from improper mold clamping or incorrect injection pressure.
Solution:
Problem: Warping happens when plastic cools unevenly, causing the bucket to lose its shape. This can occur due to issues in mold cooling or resin properties.
Solution:
Problem: Surface defects such as scratches, bubbles, or streaks can diminish the product’s appearance and quality. These defects are often caused by contamination, improper mold maintenance, or poor material flow.
Solution:
Problem: Misalignment of the mold halves during injection molding can result in dimensional inaccuracies, gaps, or parting line marks on the product. This typically happens due to worn-out alignment components or improper setup.
Solution:
Problem: Sink marks appear as small indentations on the bucket’s surface, typically where the material has not solidified properly. This often happens in thicker sections of the mold.
Solution:
Problem: Dimensional issues can occur when the plastic bucket does not match the desired specifications, resulting in incorrect sizes or distorted shapes. This can be caused by improper mold temperature, material shrinkage, or errors in mold design.
Solution:
Defects in plastic bucket molds can impact both product quality and production efficiency, but with the right approach, most issues can be resolved. Regular maintenance, proper adjustments to the injection process, and ensuring that the mold design is optimized for uniform flow and cooling are key steps in minimizing defects. By addressing these common mold problems proactively, manufacturers can improve product quality, reduce downtime, and maintain a smooth production process.
Your blog feed for digital manufacturing resources, in-depth features, and industry news.
31 Southlands Road
POLESWORTH
B78 0FL
We will reply to you in 20 minutes.
Our team is online, can be helpful for you.
Our team is online, can be helpful for you.
Didn’t find what you want? Ask our leader for help directly!