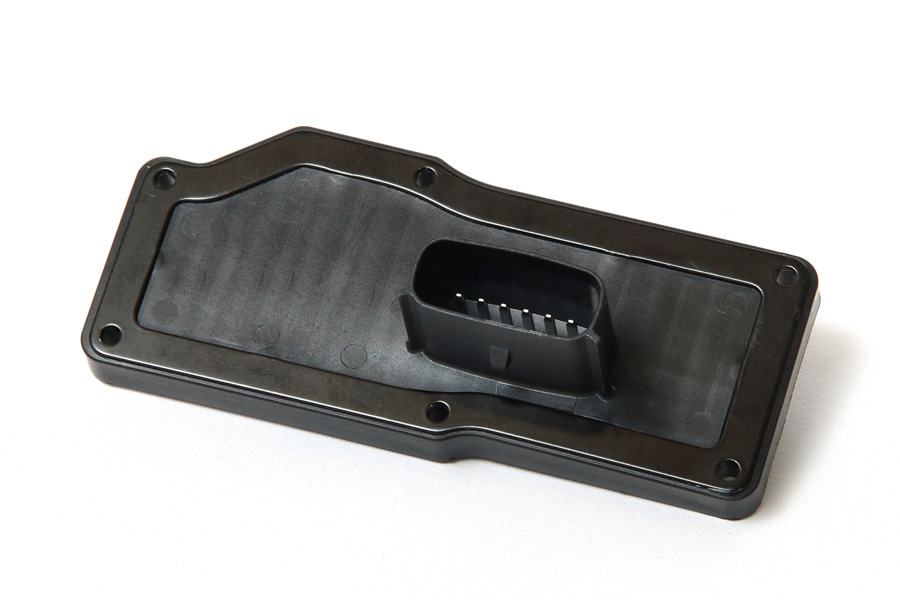
Your blog feed for digital manufacturing resources, in-depth features, and industry news.
A high-quality plastic bucket mold ensures consistent product performance, durability, and cost-effectiveness. However, achieving and maintaining that quality involves several key factors from design to production.
This article will guide you through the best practices and strategies for ensuring high-quality plastic bucket molds at every stage of the process.
The foundation of any high-quality plastic bucket begins with a well-designed mold. A robust mold design not only improves production efficiency but also ensures that the final product meets all quality standards.
Key considerations:
The material chosen for both the mold itself and the plastic being injected plays a significant role in the final product’s quality.
Mold material considerations:
The settings used during the injection molding process are crucial to achieving high-quality molds. Fine-tuning parameters can help you eliminate common issues such as warping, flash, or dimensional inaccuracies.
Key parameters to adjust:
Even the highest-quality molds need routine maintenance to ensure optimal performance. Regular inspection and care will extend the life of your molds and prevent defects in production.
Maintenance tips:
Before mass production begins, simulation software can help identify potential issues in the mold design, material flow, and injection process. Testing the mold under real-world conditions is also critical to catching any issues early.
Steps to follow:
Environmental factors, such as humidity and temperature, can also influence the quality of your molds and products. Maintaining a controlled environment helps reduce variability and prevents molding defects.
Key factors to manage:
The experience and skill of the mold maker are key factors in ensuring the quality of your molds. A well-experienced team will understand how to avoid common mistakes and optimize every aspect of the mold-making process.
What to look for:
Ensuring high-quality plastic bucket molds requires attention to detail, a focus on design, and ongoing maintenance. From the initial mold design to careful parameter adjustments, choosing the right material, and maintaining a consistent production environment, every aspect contributes to the final product’s quality. By following these best practices, manufacturers can produce plastic buckets that meet industry standards, reduce defects, and provide long-lasting durability.
Your blog feed for digital manufacturing resources, in-depth features, and industry news.
31 Southlands Road
POLESWORTH
B78 0FL
We will reply to you in 20 minutes.
Our team is online, can be helpful for you.
Our team is online, can be helpful for you.
Didn’t find what you want? Ask our leader for help directly!