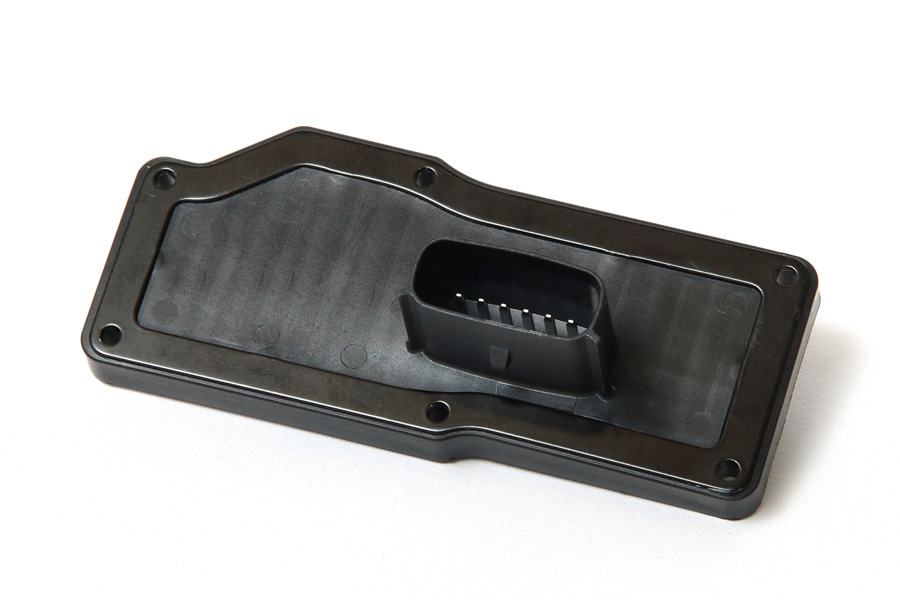
Your blog feed for digital manufacturing resources, in-depth features, and industry news.
A well-designed mold leads to smooth production and a durable final product. Here’s a step-by-step guide to designing a successful plastic bucket mold:
The first step in mold design is understanding the specific needs of the plastic bucket:
The core and cavity are the two main components of a mold that create the interior and exterior of the bucket. When designing:
The gate is where the plastic enters the mold. Its placement is crucial to ensuring smooth filling of the mold and uniform plastic distribution. Ideal gate placement helps:
Draft angles are slight inclines added to the walls of the mold. These angles help the bucket easily separate from the mold during ejection, reducing friction and minimizing damage to the product. A draft angle of 1–3 degrees is typically sufficient for most plastic bucket molds.
The ejection system is critical to ensure the easy removal of the bucket from the mold. Common ejection methods include:
Cooling is an essential part of the molding process. The faster the mold cools, the shorter the cycle time, improving production efficiency. Cooling channels should be placed close to the cavity to ensure the mold cools evenly and reduces the chances of warping.
Before full-scale production, create a prototype or use simulation software to test the mold. During testing, focus on:
After prototype testing and adjustments, finalize the mold design. Be sure to:
Designing a plastic bucket mold requires careful planning, from defining product requirements to finalizing the cooling and ejection systems. By focusing on key aspects like material choice, cavity and core design, and efficient cooling, manufacturers can create high-quality molds that lead to durable and cost-effective plastic buckets.
Your blog feed for digital manufacturing resources, in-depth features, and industry news.
31 Southlands Road
POLESWORTH
B78 0FL
We will reply to you in 20 minutes.
Our team is online, can be helpful for you.
Our team is online, can be helpful for you.
Didn’t find what you want? Ask our leader for help directly!