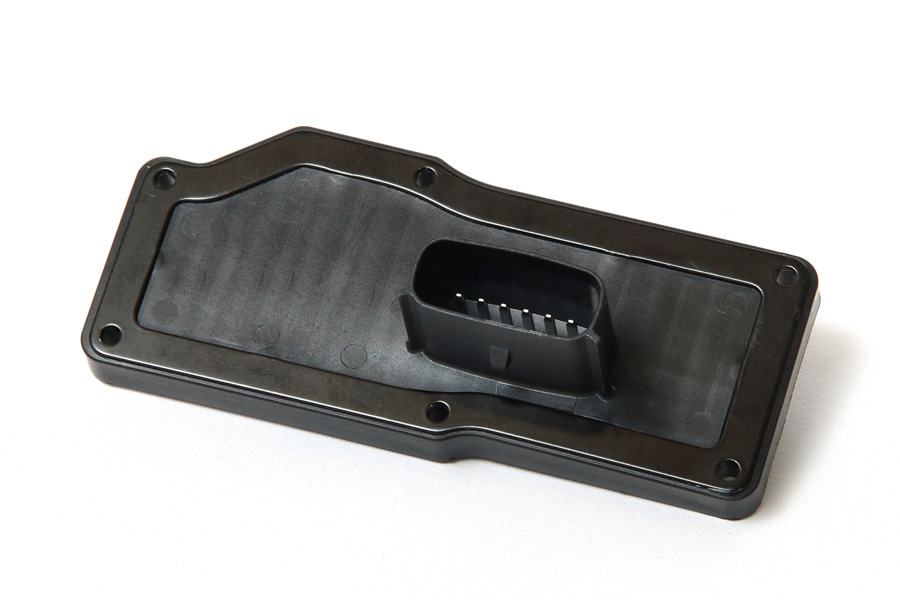
Your blog feed for digital manufacturing resources, in-depth features, and industry news.
However, like any complex manufacturing process, the production of plastic buckets can sometimes encounter issues that affect quality, efficiency, and cost. Understanding these common problems can help you troubleshoot and resolve issues quickly, ensuring smooth production and high-quality products.
In this article, we’ll explore some of the most common problems associated with plastic bucket molds and how to address them.
Over time, plastic bucket molds can experience wear and tear due to repeated use. This can lead to a variety of issues, including poor surface finish, dimensional inaccuracies, and even mold failure. Common signs of mold wear include scratches, dents, or rust on the mold surface, which can transfer to the plastic product and affect its quality.
Solution: Regular maintenance and lubrication are essential to keep molds in good condition. Conducting routine inspections and repairing any signs of wear early on can help prolong the mold’s lifespan and maintain product quality.
A common problem with plastic bucket molds is inconsistent wall thickness. This occurs when the molten plastic doesn’t flow evenly through the mold, leading to certain areas being thicker than others. This can result in defects like brittleness, warping, or weak points in the bucket.
Solution: Ensuring that the mold is properly designed with even flow channels and optimized gating systems can help prevent this issue. Adjusting the temperature and pressure during injection molding can also promote uniform filling, which leads to consistent wall thickness.
A short shot occurs when the mold cavity doesn’t fill completely with plastic, resulting in an incomplete or partially formed product. This is a common issue in plastic bucket molding, often caused by insufficient injection pressure or poor material flow.
Solution: To fix this, you may need to adjust injection settings, such as increasing the injection pressure or mold temperature. Another option is to optimize the venting system to ensure air is effectively vented out of the mold, allowing the plastic to flow more easily.
Flash is the thin layer of excess plastic that forms around the edges of the mold, typically in areas where the mold doesn’t seal properly. Flashing can cause issues with the final product’s appearance and can make the buckets harder to use or stack.
Solution: Regularly checking and maintaining the mold clamping system is essential to prevent flash. Ensure that the mold halves close properly and that there is even pressure across the entire mold. Additionally, using the right amount of material and ensuring proper cooling can help reduce flash.
Plastic bucket molds can also suffer from warping or distortion due to uneven cooling or improper mold design. Warping occurs when the plastic cools unevenly, causing the bucket to lose its shape or develop undesirable bends.
Solution: To prevent warping, ensure the cooling system is well-designed to distribute coolant evenly across the mold. Post-cooling or letting the product cool naturally before demolding can also help maintain shape stability.
A rough or inconsistent surface finish on plastic buckets is often caused by contaminants, poor mold maintenance, or improper injection molding settings. In some cases, the material itself can leave visible imperfections, such as bubbles, marks, or streaks on the final product.
Solution: Regularly clean and maintain the mold to avoid contamination. Also, optimizing the temperature and injection speed can help achieve a smoother finish. If surface imperfections are caused by the material, consider switching to a higher-quality resin or adjusting the blend of materials.
Mold alignment problems occur when the mold halves don’t align properly during injection, leading to dimensional inaccuracies or defects in the plastic bucket. This misalignment can be caused by a variety of factors, including worn-out components, incorrect setup, or mechanical failure.
Solution: Ensure the mold is properly aligned before each cycle. Regularly check the guide pins and bushings for wear, and replace them as needed. Proper mold setup and adjustment will minimize alignment issues and help produce accurate, high-quality buckets.
Contamination of materials can significantly affect the quality of plastic bucket molds. Foreign materials, such as dirt, dust, or other plastics, can cause defects like discoloration, weakness, or poor surface finish in the molded product.
Solution: Properly storing and handling materials, along with using clean injection molding machines, can help reduce contamination. Regularly cleaning both the machine and the mold itself will help maintain the integrity of the product and the mold.
Molds can sometimes overheat during the injection process, especially if the cooling system is not functioning properly. Overheating can cause issues like material degradation, dimensional shifts, or incomplete fills.
Solution: Ensure that the cooling system is working efficiently and that the mold temperature is regulated properly. If necessary, adjust the cooling channels or improve air circulation to prevent overheating.
Understanding the common problems that can arise with plastic bucket molds is key to maintaining a smooth and efficient manufacturing process. Regular mold maintenance, proper design, and fine-tuning injection molding parameters can go a long way in preventing these issues and improving product quality. By addressing these common problems early, manufacturers can minimize downtime, reduce costs, and ensure high-quality plastic buckets that meet customer expectations.
Your blog feed for digital manufacturing resources, in-depth features, and industry news.
31 Southlands Road
POLESWORTH
B78 0FL
We will reply to you in 20 minutes.
Our team is online, can be helpful for you.
Our team is online, can be helpful for you.
Didn’t find what you want? Ask our leader for help directly!