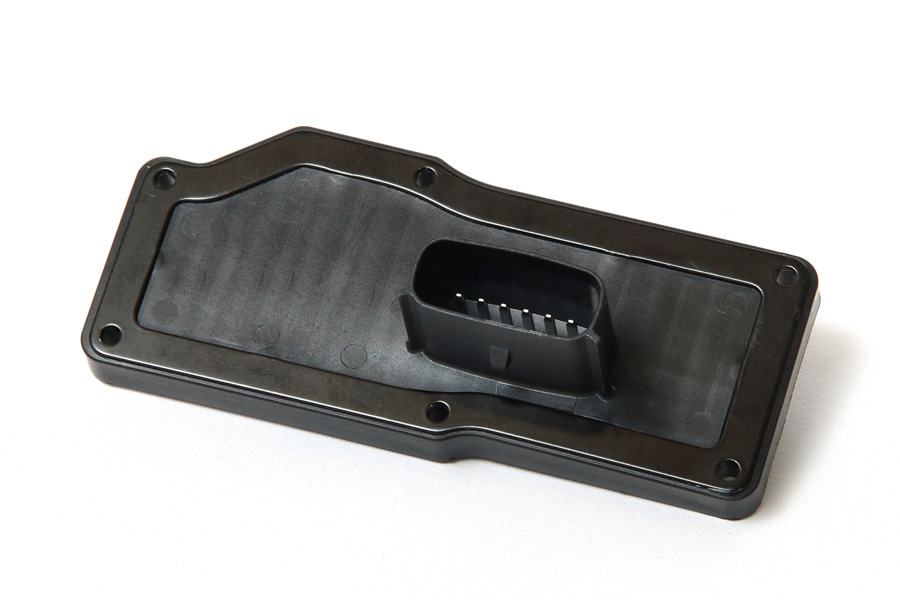
Your blog feed for digital manufacturing resources, in-depth features, and industry news.
A well-designed mold ensures high-quality buckets, cost-effective manufacturing, and smooth operations. Here are the key factors to consider when designing a plastic bucket mold:
The type of plastic material used for the bucket directly affects the mold design. Common materials for plastic buckets include:
The size, shape, and volume of the plastic bucket will influence the design of the mold. Consider the following:
The gate is where the molten plastic enters the mold. The location and type of gate can significantly impact the quality of the final product. Consider:
Efficient cooling is essential for reducing cycle time and maintaining consistent product quality. The cooling system should:
Draft angles are essential for the smooth ejection of the bucket from the mold. These slight angles on the mold walls reduce friction and help the product separate easily. Typically, a 1–3° draft angle is recommended for most designs.
The ejection system is responsible for removing the plastic bucket from the mold after it has cooled. A well-designed ejection system ensures that the bucket is released without damage. Common methods include:
Molds are a significant investment, so it’s essential to design them for durability and ease of maintenance. Consider:
Accurate tolerances are crucial for ensuring that the bucket fits together correctly and meets product specifications. Tight tolerances ensure consistent quality and prevent defects such as warping or dimensional inaccuracies.
Designing a mold should also consider the overall cost. Efficient mold design minimizes material waste, reduces cycle time, and lowers maintenance costs, helping to keep production costs down while maintaining product quality.
Design the mold with safety and environmental sustainability in mind. Ensure that the mold does not create hazardous by-products and that the entire manufacturing process meets safety standards.
Designing a plastic bucket mold requires careful attention to material selection, cooling efficiency, gate placement, ejection systems, and durability. By focusing on these factors, manufacturers can create high-quality molds that produce durable, cost-effective plastic buckets with minimal defects. Keep these considerations in mind to ensure efficient production and consistent results.
Your blog feed for digital manufacturing resources, in-depth features, and industry news.
31 Southlands Road
POLESWORTH
B78 0FL
We will reply to you in 20 minutes.
Our team is online, can be helpful for you.
Our team is online, can be helpful for you.
Didn’t find what you want? Ask our leader for help directly!