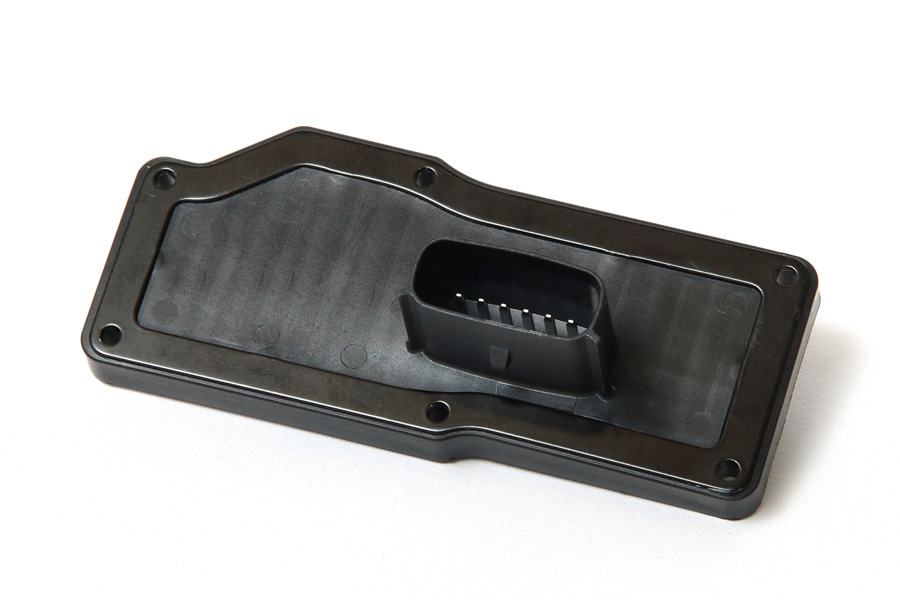
Your blog feed for digital manufacturing resources, in-depth features, and industry news.
The mold is the heart of the injection molding process, and its design and manufacturing standards directly impact the strength, durability, and precision of the finished product. Ensuring that plastic bucket molds meet the right quality standards is essential for long-lasting performance, cost-effectiveness, and customer satisfaction.
In this article, we will explore the key quality standards that plastic bucket molds should meet and why they matter in the production process.
The materials used in the mold itself play a crucial role in determining the mold’s durability and longevity. High-quality molds are typically made from robust metals that can withstand the pressures of the injection molding process and the abrasive nature of the plastics being used.
Key material standards include:
One of the primary quality standards for plastic bucket molds is dimensional accuracy. The mold must be designed and manufactured with precise measurements to ensure that the final bucket product meets specifications for size, shape, and functionality.
Why it matters:
A smooth surface finish on the mold cavity is essential for producing plastic buckets with a clean, flawless surface. A rough or poorly maintained mold can leave marks, scratches, or uneven textures on the final product.
Surface finish standards include:
A high-quality plastic bucket mold is built to last, even under high-volume production conditions. The mold should be durable enough to handle the stresses of the injection molding process without losing its shape, leading to consistent product quality over time.
Durability standards include:
Efficient plastic flow and cooling are critical for producing high-quality plastic buckets. If the mold’s flow and cooling systems are poorly designed or not functioning properly, it can lead to defects such as uneven filling, warping, or inconsistent wall thickness.
Flow and cooling standards:
Proper venting is crucial in ensuring that air and gases trapped inside the mold cavity can escape during the injection process. If air is not removed correctly, it can cause defects like air pockets or short shots, negatively impacting the quality of the plastic bucket.
Venting standards:
To ensure that plastic bucket molds meet the highest quality standards, manufacturers often comply with international industry standards. These standards outline the best practices for mold design, material selection, and quality control.
Common industry standards:
Before the mold enters full-scale production, thorough testing and inspection should be conducted to verify its quality. This process ensures that all specifications are met, and potential defects are identified early on.
Inspection steps:
Ensuring that plastic bucket molds meet high-quality standards is essential for producing durable, reliable, and cost-effective products. From selecting the right materials and designing precise molds to maintaining a consistent manufacturing process and adhering to industry standards, each step plays a critical role in achieving the highest quality plastic buckets. By focusing on these standards, manufacturers can minimize defects, increase production efficiency, and deliver high-quality products that meet customer expectations.
Your blog feed for digital manufacturing resources, in-depth features, and industry news.
31 Southlands Road
POLESWORTH
B78 0FL
We will reply to you in 20 minutes.
Our team is online, can be helpful for you.
Our team is online, can be helpful for you.
Didn’t find what you want? Ask our leader for help directly!