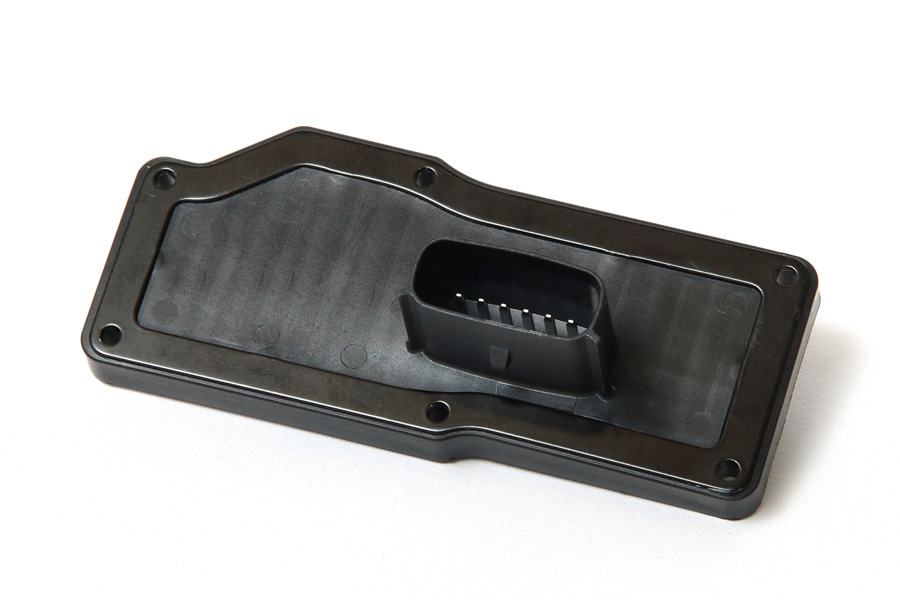
Your blog feed for digital manufacturing resources, in-depth features, and industry news.
It allows for the efficient creation of intricate and durable furniture parts. If you’re considering using injection molding for your furniture production, it’s essential to understand the steps involved. In this article, we break down the key stages of the furniture injection molding process.
Before beginning the actual injection molding process, the first step is designing the furniture component. This involves working closely with designers and engineers to create detailed 3D models of the parts, such as chair legs, table frames, or storage solutions. A prototype may be made to test the design’s functionality and appearance, allowing for adjustments before moving to mass production.
Once the design is finalized, the next step is to create the mold. The mold is the heart of the injection molding process, as it shapes the molten plastic into the final component. The mold is typically made from durable materials like steel or aluminum and is designed to withstand the high pressures involved in injection molding. Precise engineering ensures that the mold will create high-quality and consistent parts every time.
Choosing the right material is critical for achieving the desired properties of the furniture part, such as strength, durability, and flexibility. Common materials used in furniture injection molding include polypropylene, polycarbonate, and ABS plastic. These materials are chosen based on the part’s intended use, whether it’s for structural strength or aesthetic appeal. The material is then prepared for injection by melting it into a liquid form.
During the injection process, the molten plastic is injected into the mold under high pressure. The plastic is forced into every corner and crevice of the mold, ensuring that the component takes its intended shape. The pressure used is crucial for ensuring that the material flows smoothly into the mold and fills it completely. Once injected, the plastic is left to cool and solidify in the mold.
Cooling is a crucial step that ensures the plastic part retains its shape and strength. As the molten plastic cools, it hardens and takes on the precise form of the mold. The cooling time depends on the size and complexity of the part, as well as the type of material used. This step ensures that the furniture component is solid and ready for the next stage.
Once the plastic has cooled and solidified, the mold opens, and the part is ejected. The ejection process is designed to gently remove the part from the mold without causing any damage. Depending on the complexity of the design, the part may require additional steps, such as trimming or cleaning, to remove excess material or smooth out rough edges.
After the part is ejected, it undergoes thorough inspection and quality control. The manufacturer checks the part for any defects, such as warping, cracking, or inconsistencies in shape. If any issues are identified, adjustments can be made to the mold or the process to ensure that the final product meets the required standards. Quality control ensures that the furniture parts are durable, safe, and ready for use.
Depending on the specific requirements of the furniture component, post-processing steps may be necessary. This can include adding finishing touches such as painting, coating, or texturing to enhance the appearance and functionality of the part. For example, parts may be sanded or polished to achieve a smooth finish or painted for added aesthetic appeal.
For some furniture products, individual molded parts may be assembled into a final piece. The assembly process may involve joining multiple plastic parts together, such as attaching a molded chair seat to its legs or assembling a modular table frame. The use of injection-molded components in furniture assembly helps streamline production and reduces the need for additional manufacturing processes.
Finally, the completed furniture parts are carefully packaged for distribution. Depending on the order, these parts may be shipped individually or as part of a larger set of components for assembly. Efficient packaging ensures that the parts are protected during transportation and arrive in excellent condition for assembly or sale.
The furniture injection molding process involves several key steps, from design and mold creation to material injection and post-processing. Each stage is essential for creating durable, high-quality plastic parts that can be used in a variety of furniture products. By understanding the steps involved in injection molding, furniture manufacturers can ensure that their products meet both functional and aesthetic standards, leading to better outcomes for their customers. Whether for chairs, tables, or storage solutions, injection molding is a highly effective method for producing precise and reliable furniture components.
Your blog feed for digital manufacturing resources, in-depth features, and industry news.
31 Southlands Road
POLESWORTH
B78 0FL
We will reply to you in 20 minutes.
Our team is online, can be helpful for you.
Our team is online, can be helpful for you.
Didn’t find what you want? Ask our leader for help directly!