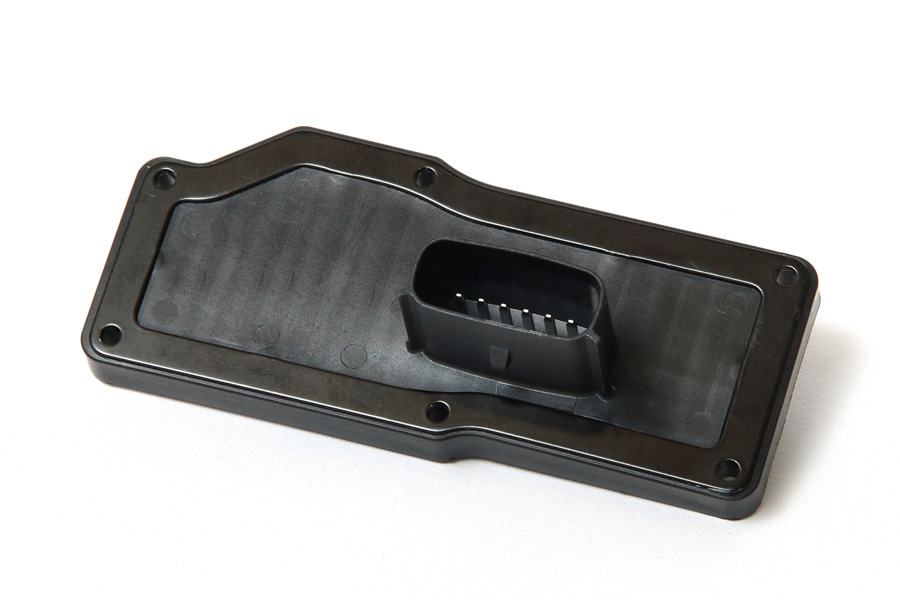
Your blog feed for digital manufacturing resources, in-depth features, and industry news.
Whether you need buckets for industrial, commercial, or consumer use, the mold manufacturing process is critical for ensuring precision, consistency, and cost-effectiveness.
In this article, we’ll break down the plastic bucket mold manufacturing process, explaining each key step and highlighting the factors that contribute to successful mold creation.
The first step in the plastic bucket mold manufacturing process is the design phase. This is where the shape, size, and features of the plastic bucket are determined. A skilled design engineer works closely with the client to understand the requirements and preferences for the final product.
Once the design is finalized, the mold construction begins. This phase involves creating the physical mold based on the digital CAD model.
Once the mold is built, it undergoes testing to ensure it functions as expected. This testing process is crucial for identifying any design flaws or issues before mass production begins.
After successful testing and adjustments, the mold is ready for full-scale production. The mold is installed into an injection molding machine, and the plastic injection process begins.
After the plastic is injected into the mold, it needs time to cool and harden before being removed. The cooling process is essential for maintaining the structural integrity and shape of the bucket.
Once the buckets are ejected from the mold, they undergo a post-processing phase. This includes trimming any excess plastic, removing flash (excess material left over from the injection process), and performing quality control checks.
Finally, the plastic buckets are packaged and prepared for shipment. This phase ensures that the buckets are safely packed to avoid damage during transportation.
The plastic bucket mold manufacturing process is a highly precise and intricate procedure that involves multiple stages, from design and engineering to testing, production, and post-processing. By using advanced technology, such as 3D modeling and CNC machining, manufacturers can create molds that produce durable, consistent, and high-quality buckets.
Understanding the process allows businesses to make informed decisions about mold design, material selection, and production methods. Whether you need a small batch of customized buckets or large volumes for industrial use, plastic injection molding ensures efficiency, cost-effectiveness, and high-quality results every time.
By working with a trusted mold manufacturer, you can ensure that your plastic buckets are made to meet your specific needs and will stand the test of time.
Your blog feed for digital manufacturing resources, in-depth features, and industry news.
31 Southlands Road
POLESWORTH
B78 0FL
We will reply to you in 20 minutes.
Our team is online, can be helpful for you.
Our team is online, can be helpful for you.
Didn’t find what you want? Ask our leader for help directly!