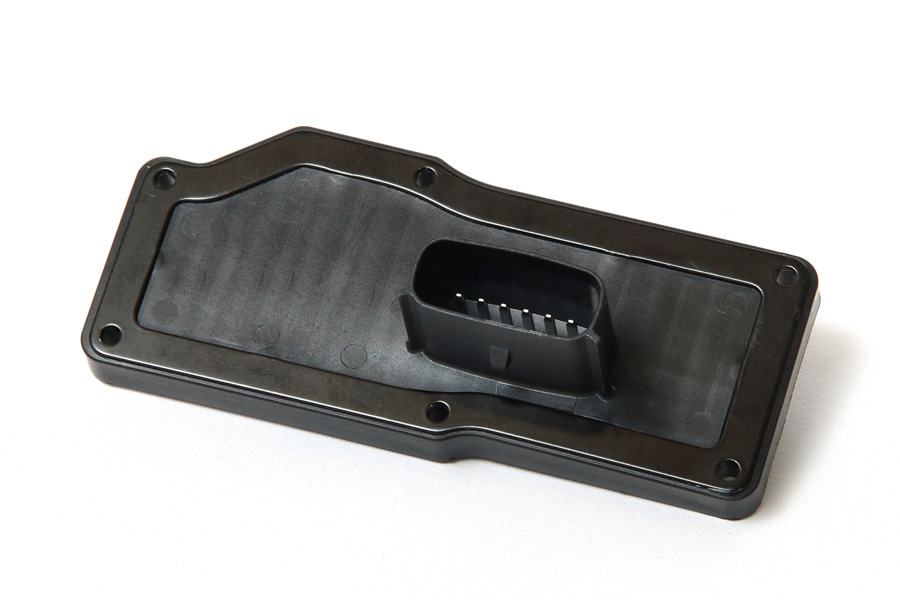
Your blog feed for digital manufacturing resources, in-depth features, and industry news.
Two common approaches are injection molding and traditional furniture manufacturing. Each method has its own set of advantages, and choosing the right one depends on factors like design complexity, production volume, and material needs. In this article, we’ll explore the differences between injection molding and traditional furniture manufacturing to help you make an informed decision.
Injection molding is a highly efficient manufacturing process where molten plastic is injected into a mold to create a part. Once the plastic cools, the mold opens, and the part is ejected. This method allows for high-volume production of intricate designs with consistent quality. Injection molding is ideal for creating plastic furniture components such as chair seats, backs, tables, and storage solutions.
Traditional furniture manufacturing refers to the processes used for creating furniture with methods like woodcraft, metalworking, and upholstery. These techniques involve cutting, shaping, joining, and finishing materials to build furniture pieces. Wood, metal, and sometimes fabrics are the primary materials used in traditional furniture manufacturing, and these methods are often associated with custom or handcrafted furniture.
Injection Molding: One of the greatest strengths of injection molding is its ability to produce complex and intricate designs with ease. Whether you need detailed textures, precise shapes, or geometric patterns, injection molding can handle it all. This flexibility makes it an excellent choice for modern furniture designs that require precision and creativity.
Traditional Manufacturing: While traditional manufacturing techniques allow for custom designs, they are typically more limited in complexity. Cutting and shaping materials like wood and metal require more manual effort and may be harder to achieve with high precision.
Injection Molding: The primary material used in injection molding is plastic, which can be tailored to meet specific needs. Plastics such as ABS, polypropylene, and polycarbonate are commonly used for producing strong, lightweight, and durable furniture parts. Additionally, plastics can be molded into various colors and finishes to suit different design preferences.
Traditional Manufacturing: Traditional furniture manufacturing utilizes a wider range of materials, including wood, metal, glass, and fabric. These materials provide a different aesthetic and tactile experience compared to plastic but may require more maintenance and care over time.
Injection Molding: Once the mold is created, injection molding allows for rapid, high-volume production. This process can produce hundreds or even thousands of identical parts in a short time, making it ideal for mass production. The efficiency and speed of injection molding make it an excellent choice for businesses that need to scale production quickly and cost-effectively.
Traditional Manufacturing: Traditional manufacturing methods are generally slower and more labor-intensive, particularly for custom or handcrafted pieces. The production process often involves multiple steps, such as cutting, sanding, joining, and finishing, which can take more time and effort. As a result, traditional methods are typically better suited for smaller production runs or custom-made furniture.
Injection Molding: While the initial cost of creating a mold can be high, injection molding becomes highly cost-effective when producing large quantities of furniture parts. The reduced labor costs and increased production speed contribute to lower per-unit costs, making it an ideal option for mass production.
Traditional Manufacturing: Traditional methods often involve higher labor costs due to the manual work involved in cutting, shaping, and assembling. Custom pieces or small production runs can also lead to higher costs per unit. However, for high-end or artisanal furniture, the investment in labor and craftsmanship may be justified.
Injection Molding: Furniture made from injection-molded plastic is generally durable and resistant to wear and tear. Plastic furniture parts are often lightweight, weather-resistant, and easy to maintain. They can withstand environmental factors such as moisture and UV rays, making them a great choice for both indoor and outdoor furniture.
Traditional Manufacturing: Furniture made from materials like wood and metal is often very sturdy and long-lasting. However, these materials may require more maintenance to preserve their appearance and functionality over time. For example, wood may need periodic polishing or sealing, and metal may require rust protection.
Injection Molding: While injection molding allows for some degree of customization, particularly in terms of color and finish, it is generally better suited for producing uniform products in large quantities. Customization options are limited compared to traditional methods.
Traditional Manufacturing: Traditional methods excel in producing custom or one-of-a-kind furniture pieces. Woodworkers and artisans can create personalized designs based on specific customer requirements, making this method ideal for bespoke or high-end furniture.
Choosing between injection molding and traditional furniture manufacturing ultimately depends on your production needs, design requirements, and budget.
Injection molding is best suited for high-volume production, intricate plastic parts, and cost-effective manufacturing. It works well for modern, functional furniture designs that require speed, precision, and durability.
Traditional furniture manufacturing is ideal for bespoke, artisanal pieces that require craftsmanship and a wider variety of materials. It’s better for smaller runs, custom designs, and furniture that emphasizes traditional or classic aesthetics.
Both injection molding and traditional furniture manufacturing have their place in the furniture industry, with each method offering distinct advantages. By understanding the strengths and limitations of each approach, you can make an informed decision based on your specific needs. Whether you prioritize speed, cost, material diversity, or custom designs, there’s a solution that will help you achieve your desired results in furniture production.
Your blog feed for digital manufacturing resources, in-depth features, and industry news.
31 Southlands Road
POLESWORTH
B78 0FL
We will reply to you in 20 minutes.
Our team is online, can be helpful for you.
Our team is online, can be helpful for you.
Didn’t find what you want? Ask our leader for help directly!