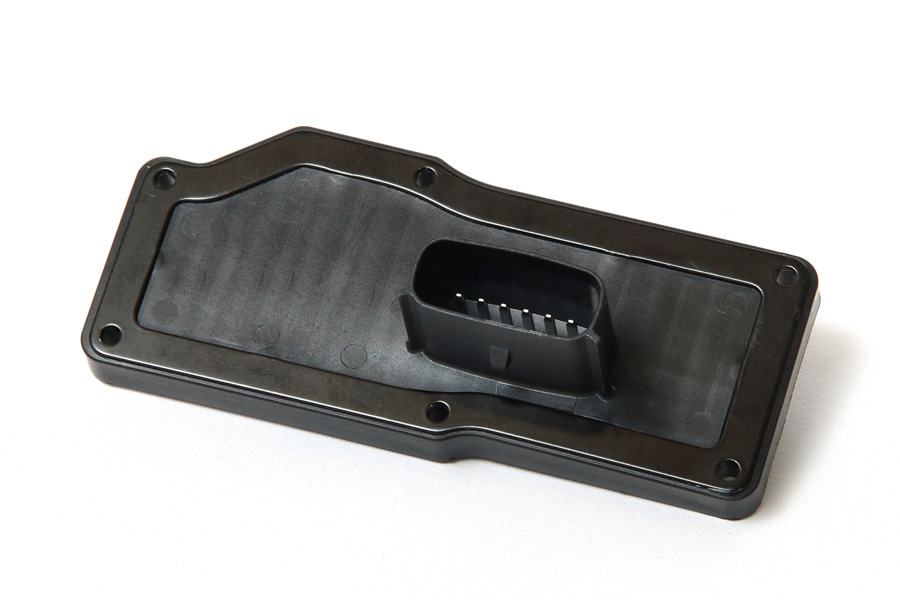
Your blog feed for digital manufacturing resources, in-depth features, and industry news.
Once set up, it can manufacture a large volume of parts per hour, from a wide range of different plastics plus other materials such as liquid silicone rubber. However, like any manufacturing process, it does have some disadvantages, and if these prove significant to the success of your project, then you may be better off exploring alternative manufacturing technologies such as 3D printing or CNC machining. In this blog, we will take you through the main advantages of injection molding and explore when it may be better for you to consider an alternative production method.
Once you have developed the molds, the process is extremely fast with cycle times as short as 10 seconds. It is excellent for medium and high-volume production runs for anything from 10,000 parts to well over 100,000 depending on what molds you use. Sometimes you can increase production by using a multi cavity or family mold, where several parts are produced from one press to further increase the manufacturing rate. If you are outsourcing your molding then it’s also important to consider an efficient front-end design and order process – take a look at our on demand manufacturing.
For high output production runs the cost per part is very low. Even for medium volumes – in the range of 10,000 to 25,000 parts, you can keep the costs down by using aluminum molds instead of steel.
You can manufacturer identical products over and over again. This is ideal when you need to have parts with high tolerances and reliability across high volumes.
There is a huge range of plastic materials that you can select from depending on what properties you need from your final part. And you are not limited to plastic, Protolabs also offers liquid silicone rubber molding.
When should you consider alternative manufacturing methods to injection molding.
If you are committing to steel mold tools for high production volumes (100,000+) then it can take a great deal of time and machining to produce and this can be a significant capital cost. If you need lower volumes of parts then this will affect your cost per part price and it may be worth exploring other options such as using aluminum molds instead.
It can take up to 12 weeks to produce steel tooling. If you need to get production running before this then take a look at our on-demand production; by using aluminum molds and digitizing our front-end process we can ship anything from 25 to 10,000+ parts in 15 working days or less from the point that you first upload your CAD. Sometimes parts shipped in as little as one day.
You will need to consider certain design elements, such as:
You also need to consider where to place your gates, ejectors and cooling lines if aesthetics are important. And remember it’s also hard to change the design of a mold – you can remove part of the mold, or add plastic to your final part, but not the other way round.
For smaller production runs, 3D printing allows you to design virtually any shape or geometry that you require. As a rapidly developing technology there is an increasing number of plastic and other materials, even metal, that we can produce.
Even if you’ve never tried it before, it’s logical to assume that working with one manufacturer throughout your product’s entire lifecycle makes sense. You gain consistency from stage to stage because learnings from one cycle can be transferred to inform the next.
Manufacturing partners like Protolabs with the capabilities needed to journey with you from prototyping to mass production—with a stop along the way for bridge production—ensures that issues that could crop up during that transition are either avoided or easily smoothed out. It also provides a fallback when supply issues crop up because you’re working with the company that has built those parts previously.
In the end, including a plan to use bridge production is something that should be baked into every product you produce. It can help rescue you in an emergency and can also be a sensible transitional phase during a typical product’s lifecycle.
Your blog feed for digital manufacturing resources, in-depth features, and industry news.
31 Southlands Road
POLESWORTH
B78 0FL
We will reply to you in 20 minutes.
Our team is online, can be helpful for you.
Our team is online, can be helpful for you.
Didn’t find what you want? Ask our leader for help directly!