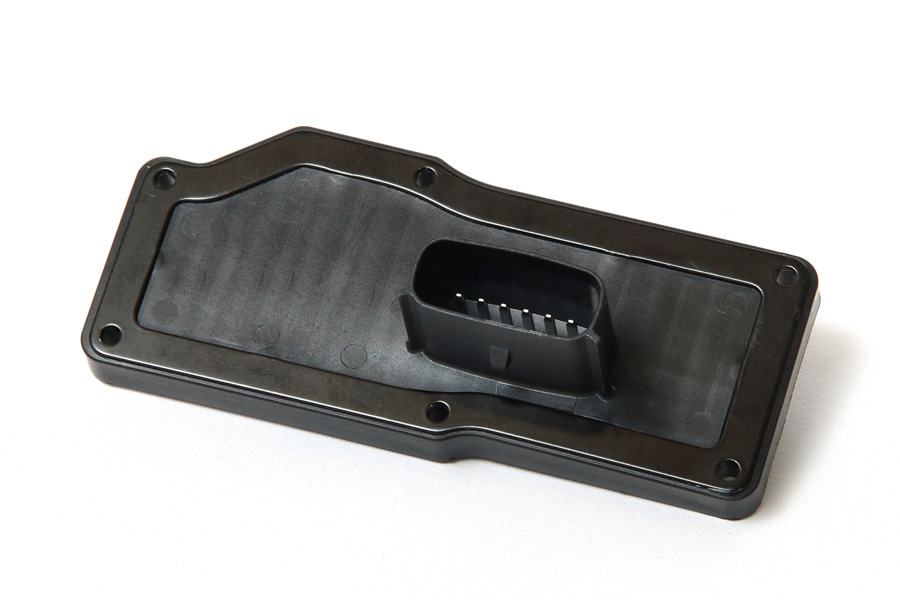
Your blog feed for digital manufacturing resources, in-depth features, and industry news.
These systems use advanced robotics and technology to streamline the molding process, improving speed, precision, and consistency while reducing costs. The move towards automation is revolutionizing production lines and is quickly becoming a game-changer for the plastic bucket industry.
Automated plastic bucket molding systems are designed to improve efficiency in manufacturing by utilizing automated machines and robotics. These systems automate key steps in the molding process, such as injecting molten plastic into molds, cooling, and ejecting the finished buckets. By minimizing human intervention, automated systems ensure high production speeds and consistently high-quality products.
Automated systems allow for continuous, 24/7 production. Unlike manual processes, these systems don’t need breaks, which results in a significant increase in output and a reduction in production time. This makes it ideal for businesses with high demand or those looking to scale up quickly.
One of the standout features of automated systems is their ability to produce uniform, high-quality products. With precise control over temperature, pressure, and speed, the systems eliminate the inconsistencies that can occur in manual molding. This means every bucket produced is of the same quality, meeting strict industry standards.
Although setting up automated molding systems can require an upfront investment, the long-term cost savings are significant. These systems reduce the need for labor, minimize waste, and improve material usage efficiency, leading to lower production costs over time.
With automation handling the majority of the tasks, companies can reduce their reliance on human labor, freeing up staff for more valuable roles. This also lowers the risk of human error, improving the overall safety and reliability of the production line.
In an automated system, molten plastic is injected into a mold via an injection molding machine. The system then cools the plastic to solidify it, and robotic arms automatically eject the completed buckets. The entire process is computer-controlled, allowing for high precision and quick changeovers between different bucket designs and sizes.
Automating the plastic bucket molding process offers a variety of benefits for businesses. By choosing automated systems, companies can increase production efficiency, reduce costs, and ensure top-quality products with minimal defects. Automation also allows for greater flexibility, as manufacturers can easily adjust to different production needs and scale their operations accordingly.
Automated plastic bucket molding systems are at the forefront of modern manufacturing. Offering benefits like improved efficiency, consistent quality, and cost savings, these systems are ideal for businesses looking to enhance their production capabilities. As the demand for plastic buckets continues to grow, automated molding systems provide a smart, future-proof solution for manufacturers seeking to stay competitive in a fast-moving market.
Your blog feed for digital manufacturing resources, in-depth features, and industry news.
31 Southlands Road
POLESWORTH
B78 0FL
We will reply to you in 20 minutes.
Our team is online, can be helpful for you.
Our team is online, can be helpful for you.
Didn’t find what you want? Ask our leader for help directly!