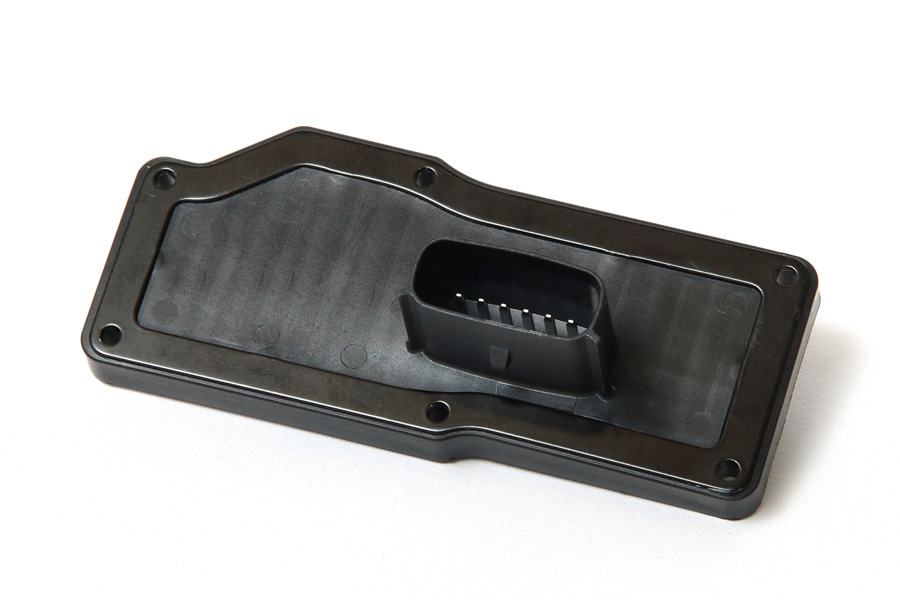
Your blog feed for digital manufacturing resources, in-depth features, and industry news.
Inconsistent flow can lead to defects such as uneven wall thickness, short shots, or warping, all of which can compromise the integrity of the finished bucket. By addressing these flow inconsistencies, manufacturers can ensure better product quality, reduce waste, and improve efficiency.
In this article, we’ll explore the causes of plastic flow inconsistencies in bucket molds and provide practical solutions to resolve these issues.
Before diving into solutions, it’s important to understand the common causes of plastic flow inconsistencies:
Addressing plastic flow issues requires a combination of proper mold design, adjusting injection settings, and ensuring consistent material quality. Here’s how you can fix these problems:
The design of your mold plays a major role in controlling plastic flow. Improperly designed gates, flow channels, or inadequate cooling systems can all lead to uneven filling. Here’s what to do:
Fine-tuning the settings of the injection molding machine can help regulate the flow of plastic and ensure a uniform fill:
Proper venting is crucial to ensure that air is able to escape from the mold as the plastic enters. Trapped air can disrupt the flow of plastic and cause inconsistencies.
The type of material you use can have a significant impact on plastic flow. Different resins have varying viscosities, which can affect how well they flow through the mold.
Uneven cooling can also affect how plastic flows and solidifies in the mold, leading to warping or inconsistent thickness. Here’s how to tackle this:
Even after resolving initial flow issues, ongoing maintenance is essential to ensure that plastic bucket molds continue to perform well over time.
Addressing plastic flow inconsistencies in bucket molds is crucial for producing high-quality products. By optimizing mold design, adjusting injection parameters, ensuring proper venting, using the right material, and maintaining a well-functioning cooling system, manufacturers can prevent flow issues that lead to defects. Regular mold inspections and maintenance will help ensure that your molds continue to operate efficiently, delivering consistent and reliable results with each production cycle.
By taking these steps, manufacturers can improve production efficiency, reduce defects, and ensure that plastic buckets meet the highest standards of quality.
Your blog feed for digital manufacturing resources, in-depth features, and industry news.
31 Southlands Road
POLESWORTH
B78 0FL
We will reply to you in 20 minutes.
Our team is online, can be helpful for you.
Our team is online, can be helpful for you.
Didn’t find what you want? Ask our leader for help directly!